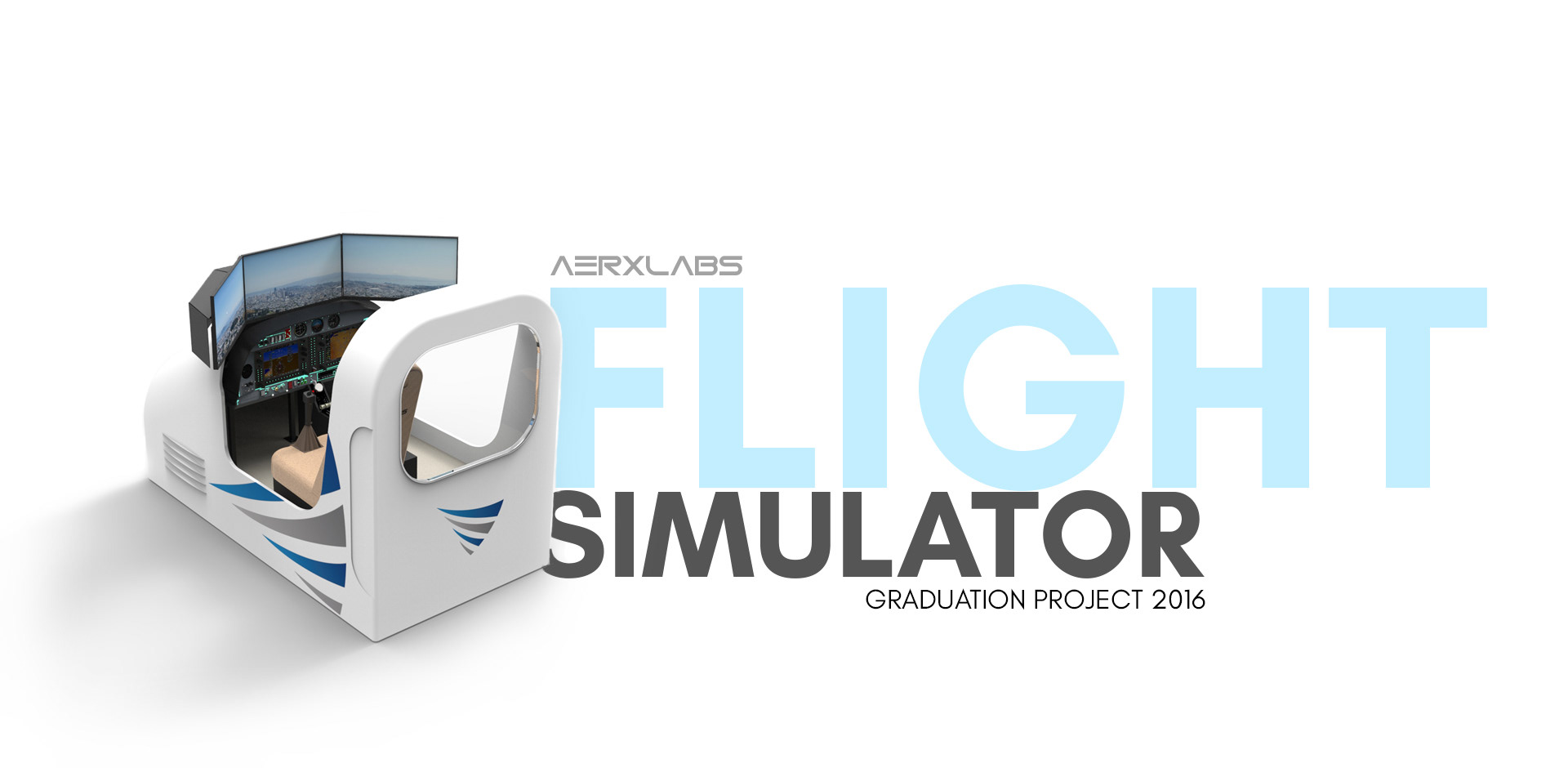
This project started as my Graduation Project in September 2015 at AerX Labs, a startup with interests in Experimental/Affordable Next Gen Avionics products and Flight Simulation(Flightrix) technologies.
I had to design a Flight Simulator for the aircraft Diamond DA42.
The Flight Simulator offers to be the best training device for an aspiring pilot or aeronautical engineers to create scenarios and serve as a learning and skill development tool.
The Flight Simulator offers to be the best training device for an aspiring pilot or aeronautical engineers to create scenarios and serve as a learning and skill development tool.
The Diamond DA42 Twin Star is a four seat, twin engine, propeller-driven airplane manufactured by Diamond Aircraft Industries. The DA42 is mainly operated by flight training schools, aerial surveillance and mapping operators.
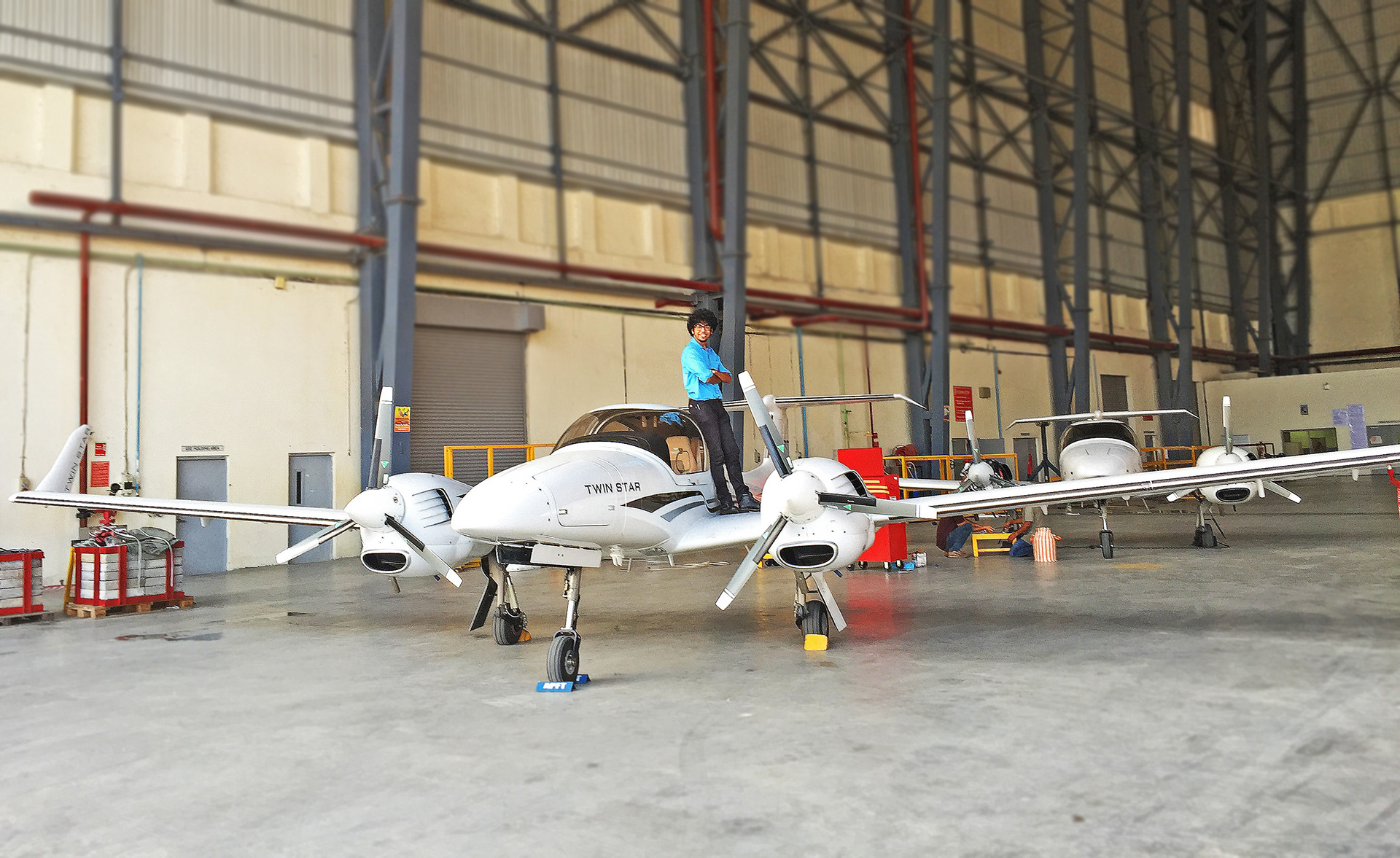
I had to study the aircraft and take accurate dimensions to replicate it later on. Luckily two Diamond DA42s were available for us to see it thoroughly at Hyderabad where they also had a DA42 Simulator for training purposes.

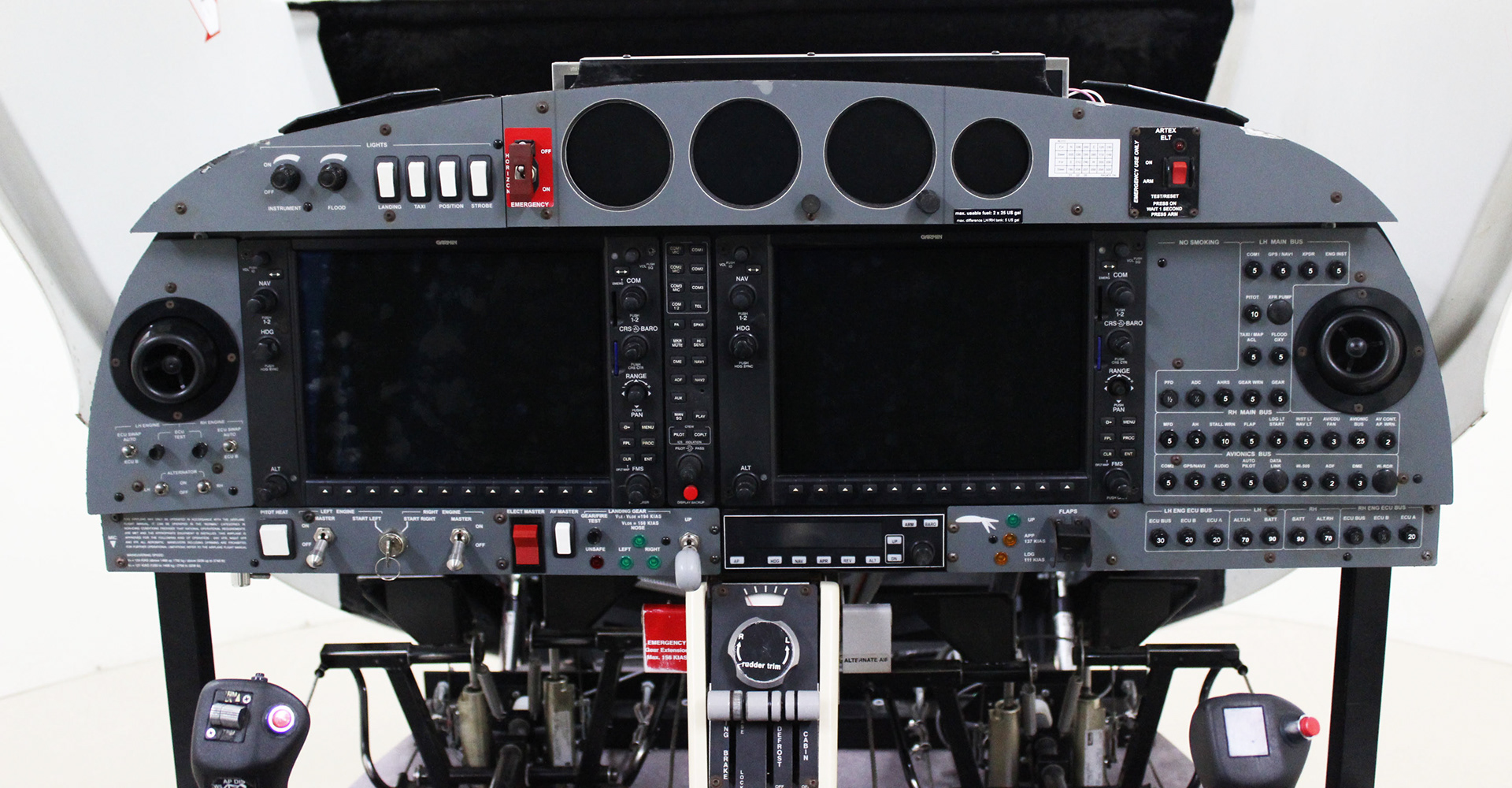
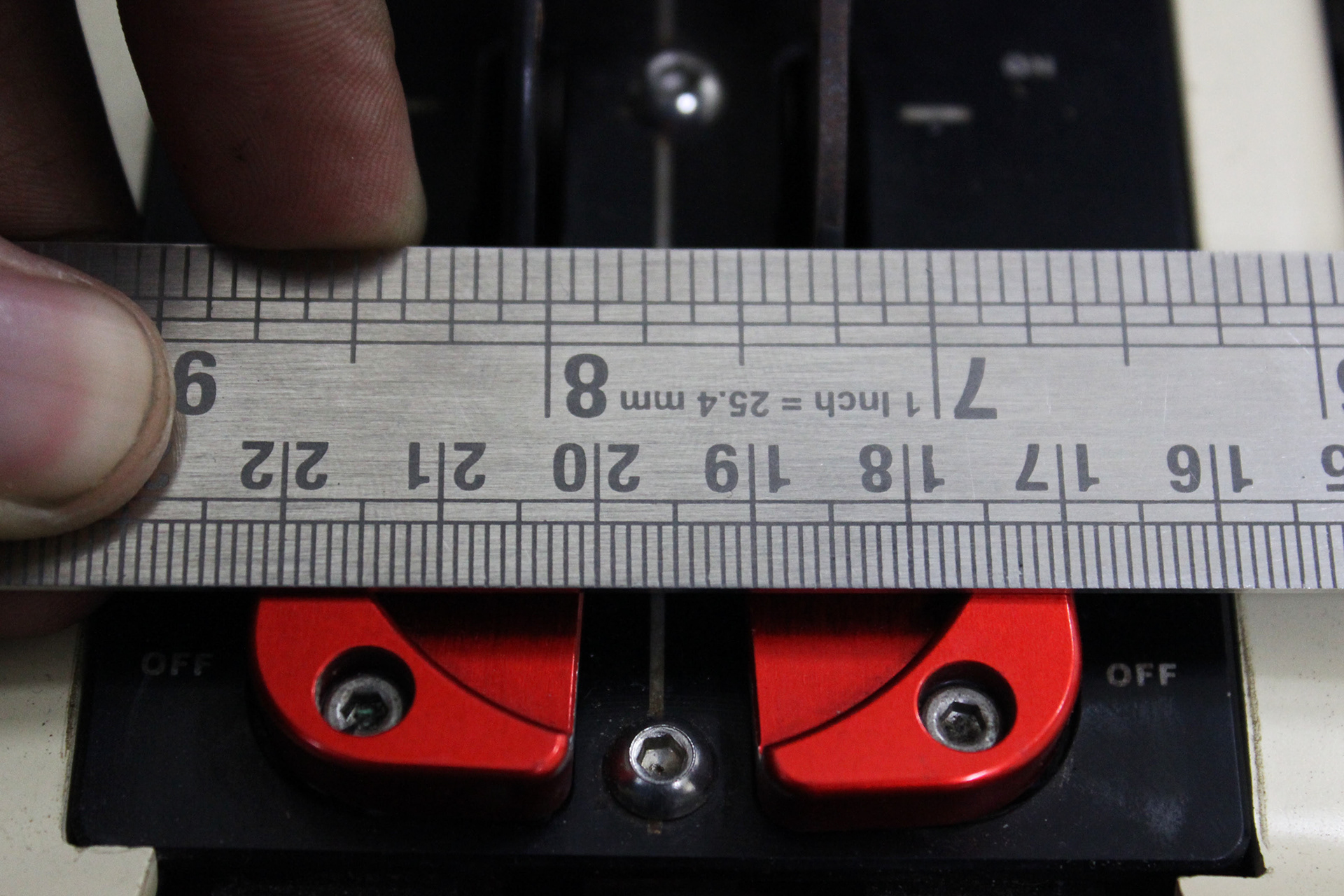
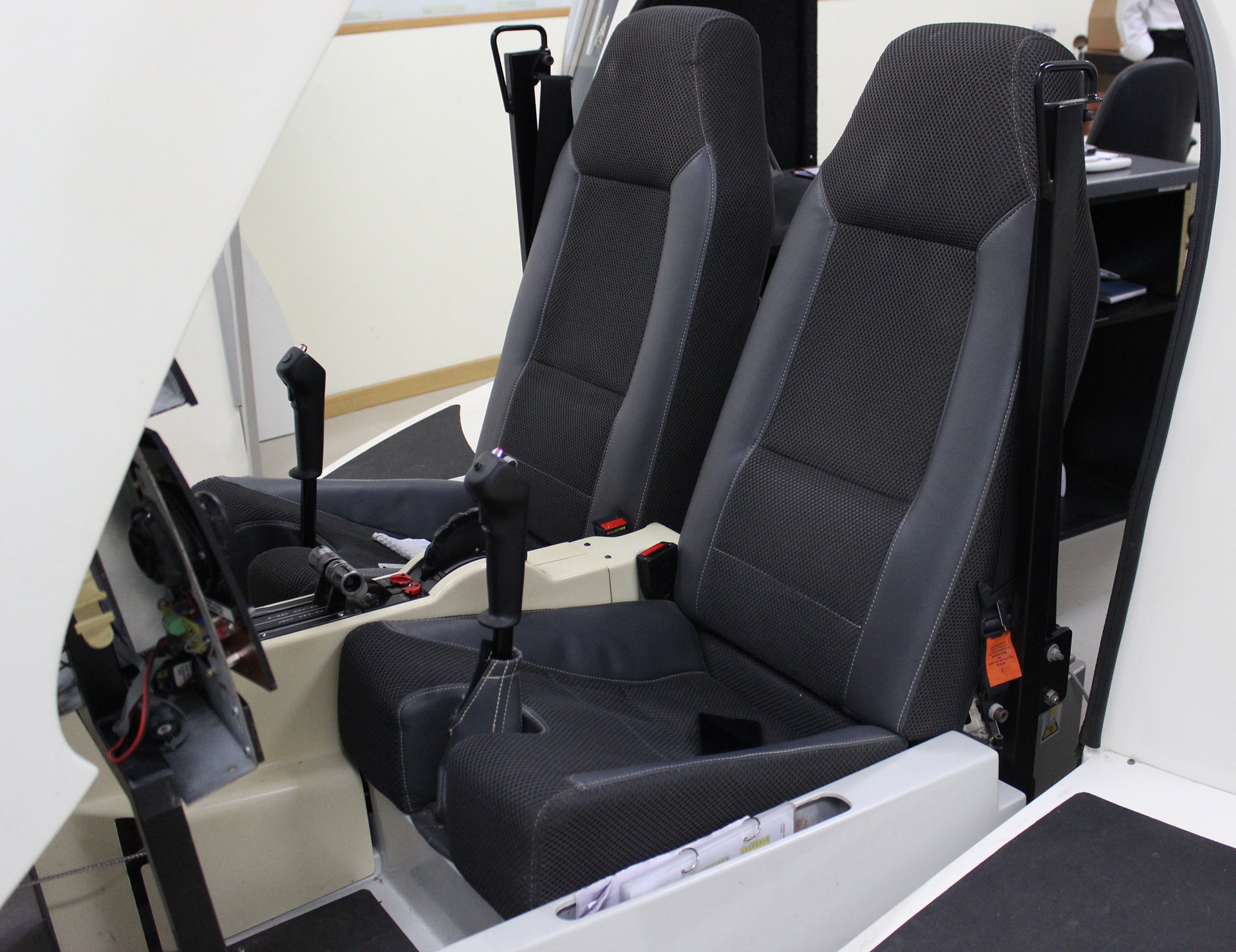
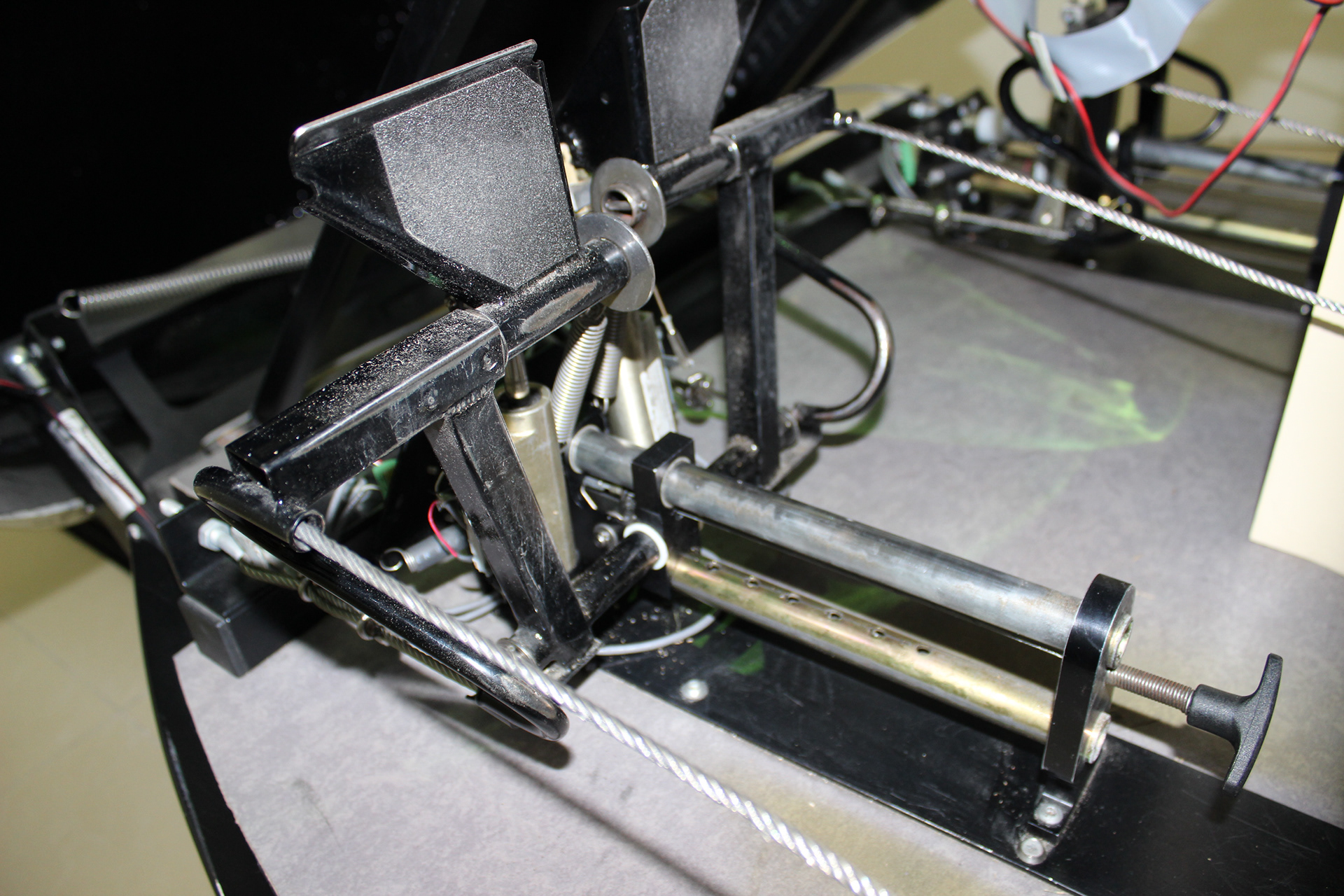
The Faceplate
The cockpit’s most important thing; the faceplate. It will be made using Aluminum
(2mm) as the base for the whole faceplate. After laser cutting it, it will be bent and will take the exact shape as the faceplate from the aircraft and then components will be added to it. There will be 3 layers in all, first being the aluminum, then Acrylic and stickers for the
Infographics.
(2mm) as the base for the whole faceplate. After laser cutting it, it will be bent and will take the exact shape as the faceplate from the aircraft and then components will be added to it. There will be 3 layers in all, first being the aluminum, then Acrylic and stickers for the
Infographics.
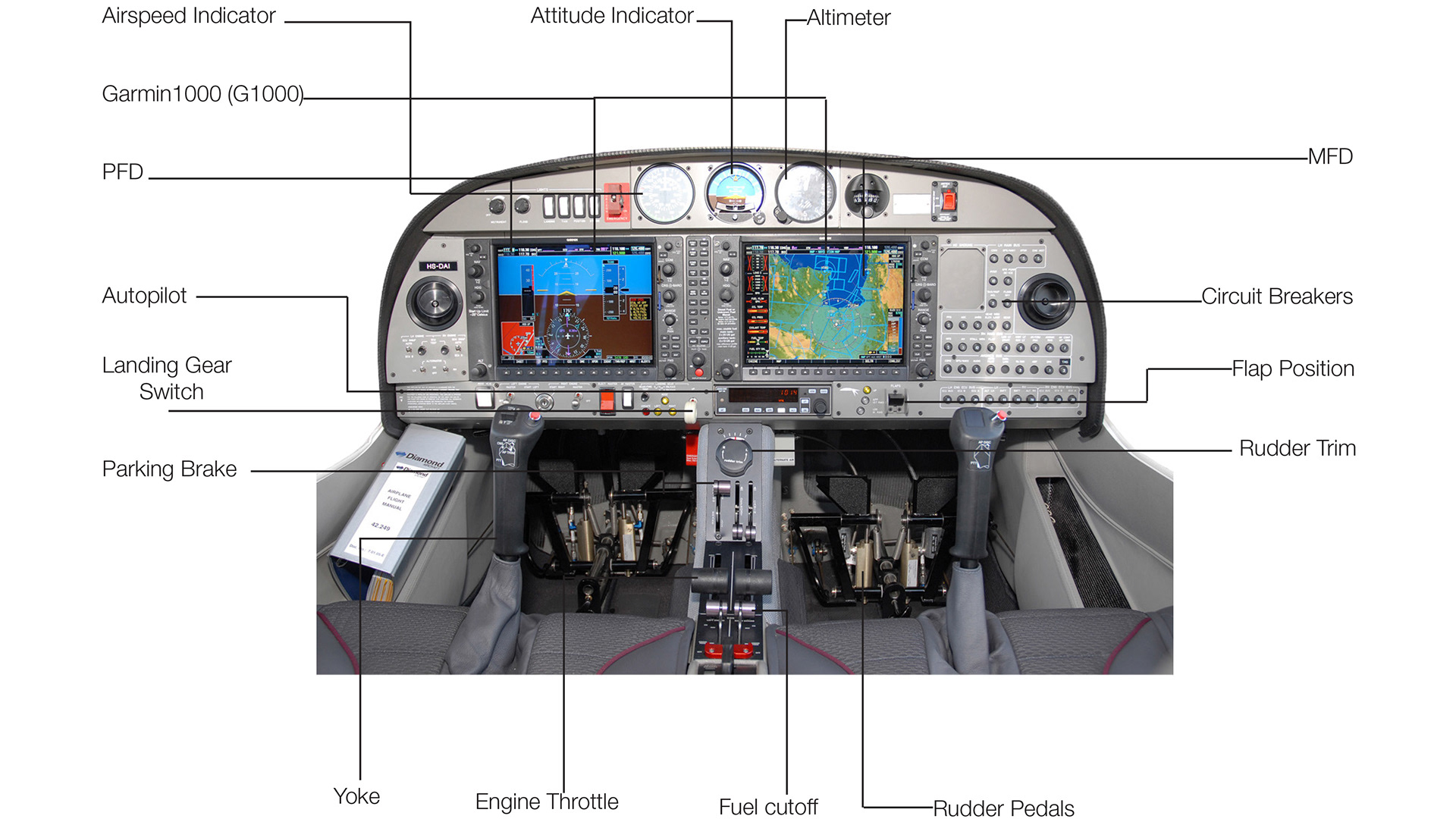
The faceplate and it's basic assembly.

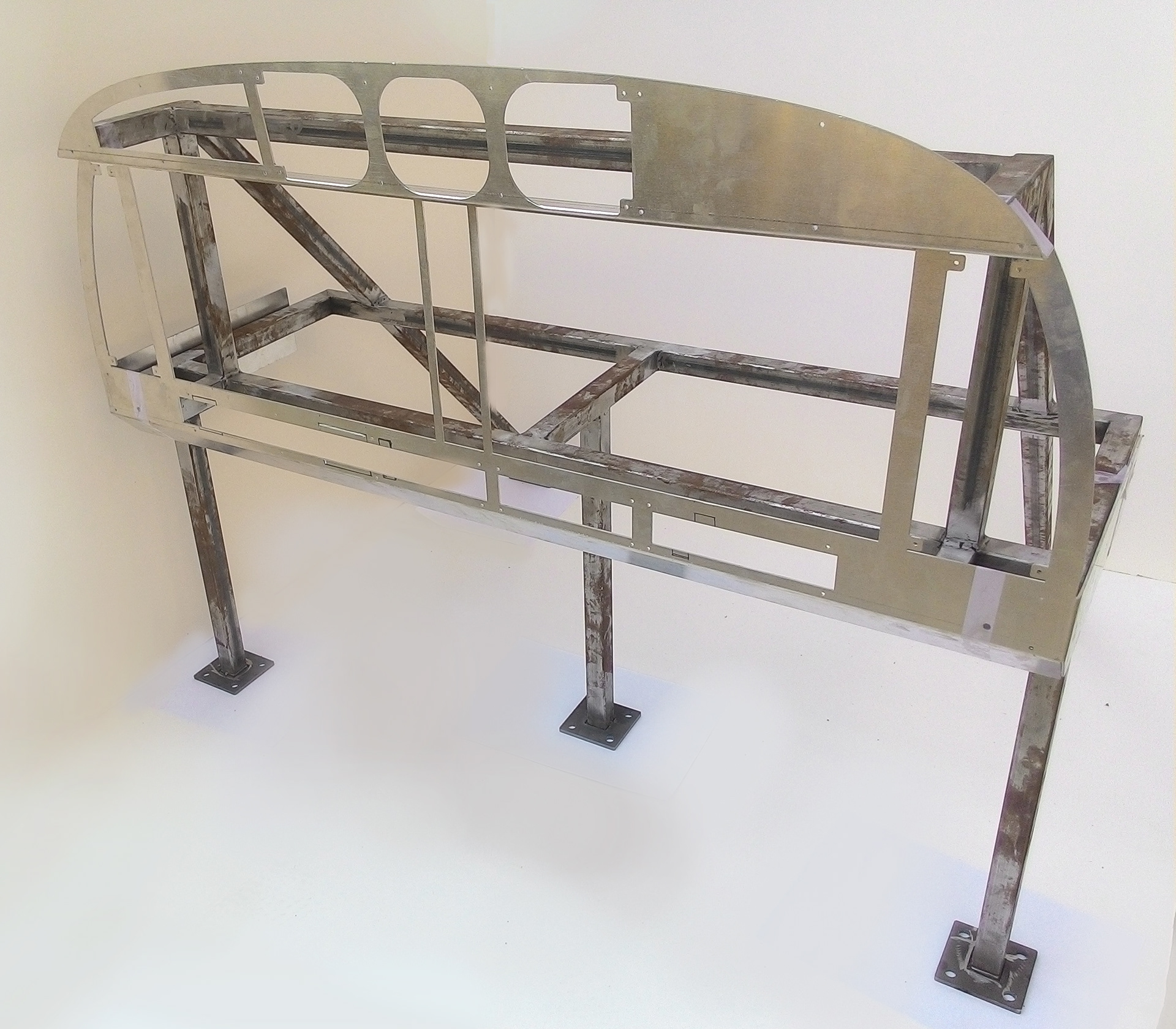
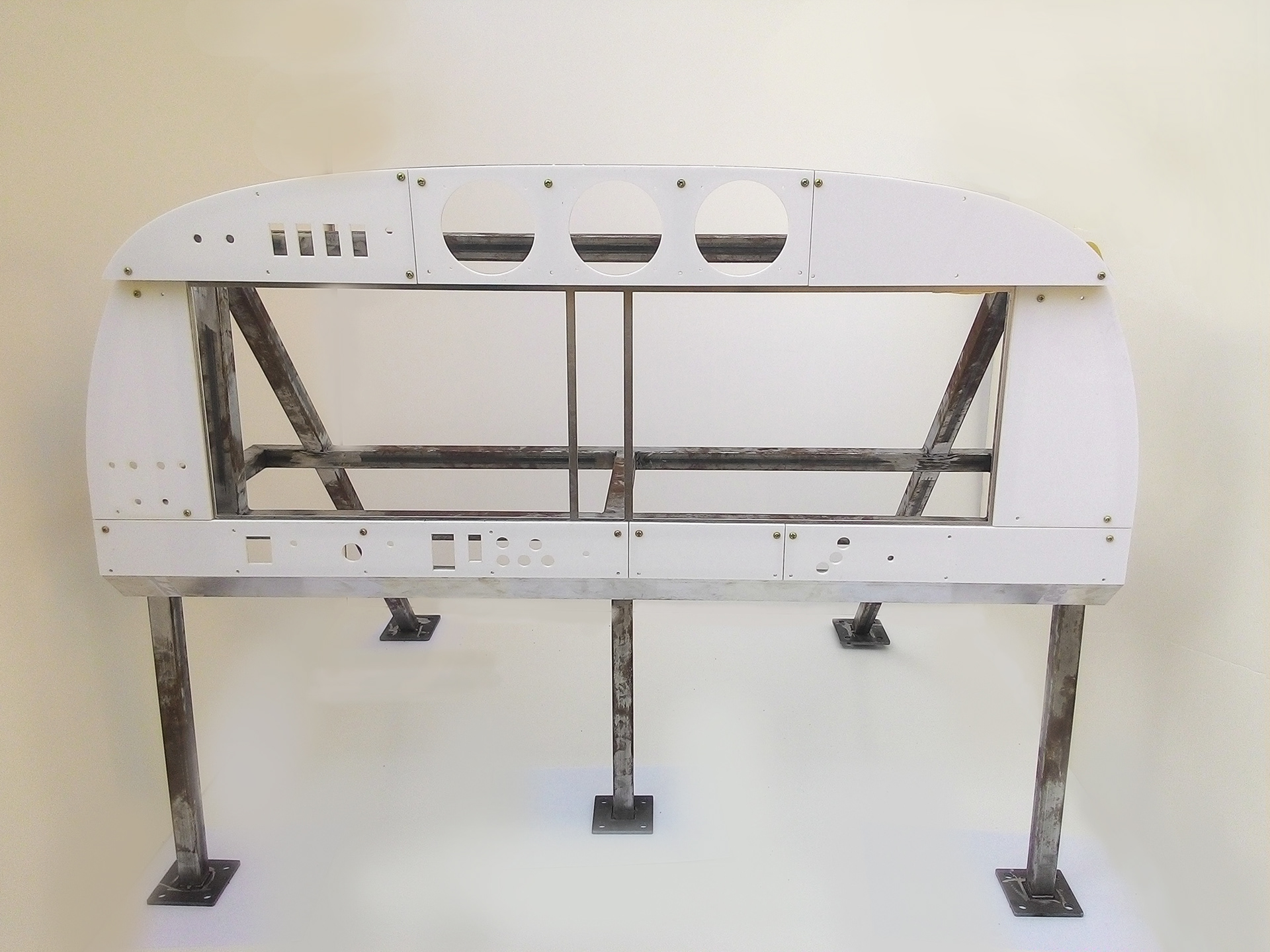
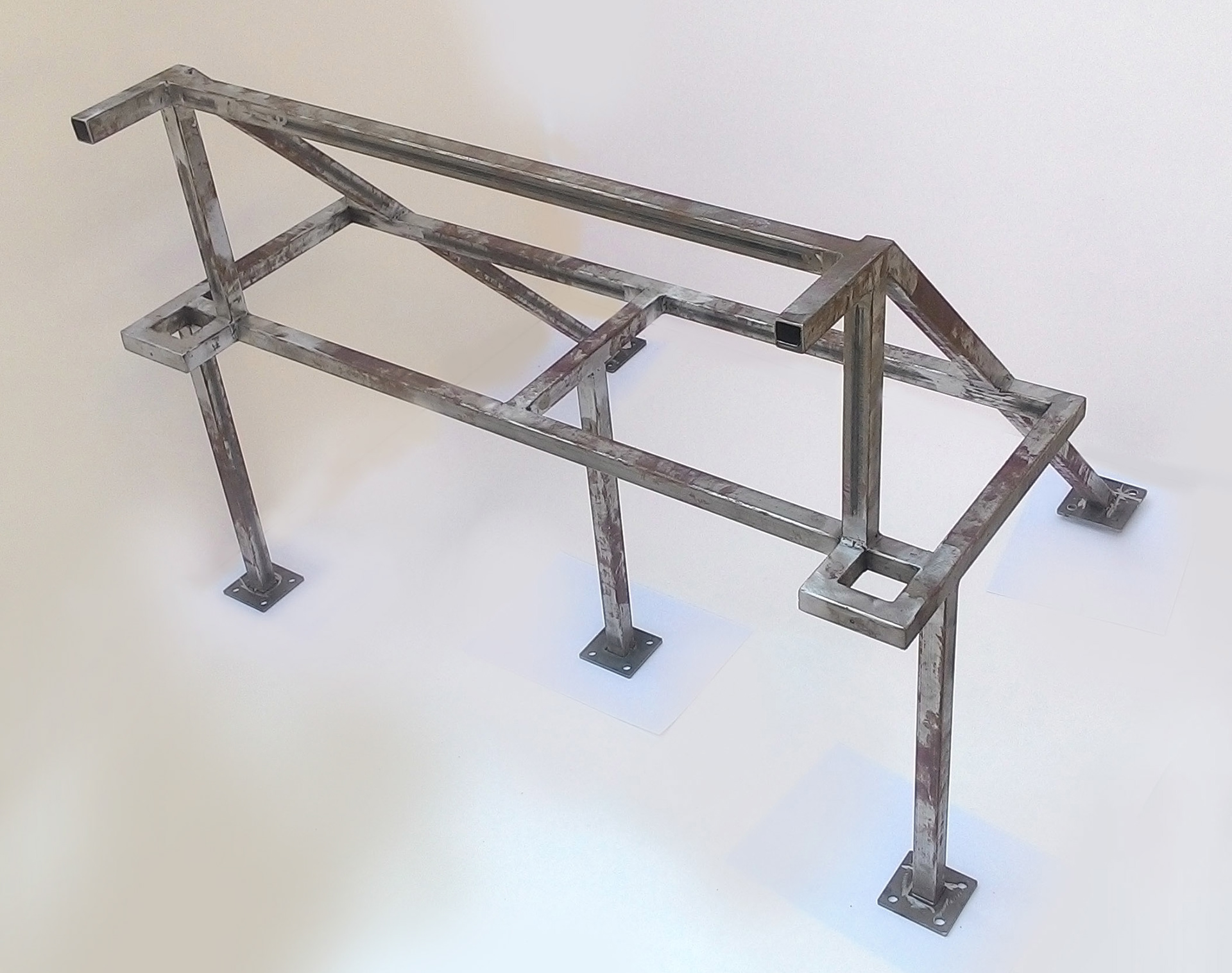
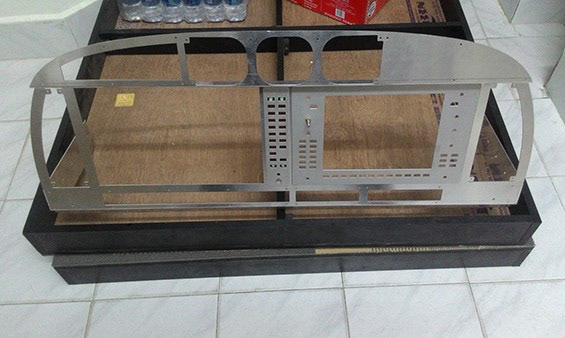

Special industrial grade vinyl prints were also created having all the details and indicators similar to the cockpit of the DA42 aircraft (top).
The AFD1080G unit used as PFDs (Primary Flight Display) and MFDs (Multi-function Display) developed by AerX Labs and Airspeed Indicator, Attitude Indicator and Altimeter.
The AFD1080G unit used as PFDs (Primary Flight Display) and MFDs (Multi-function Display) developed by AerX Labs and Airspeed Indicator, Attitude Indicator and Altimeter.
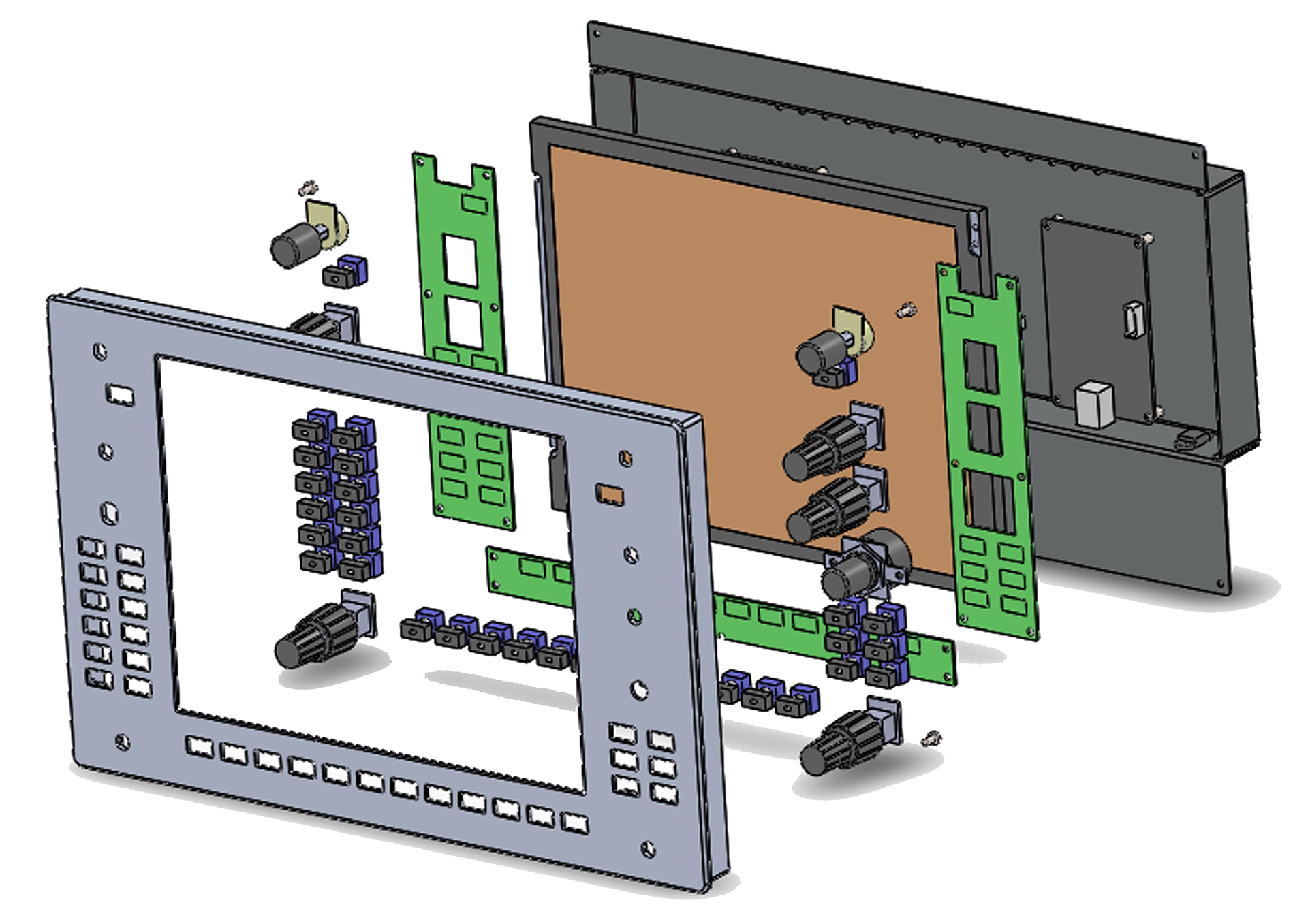
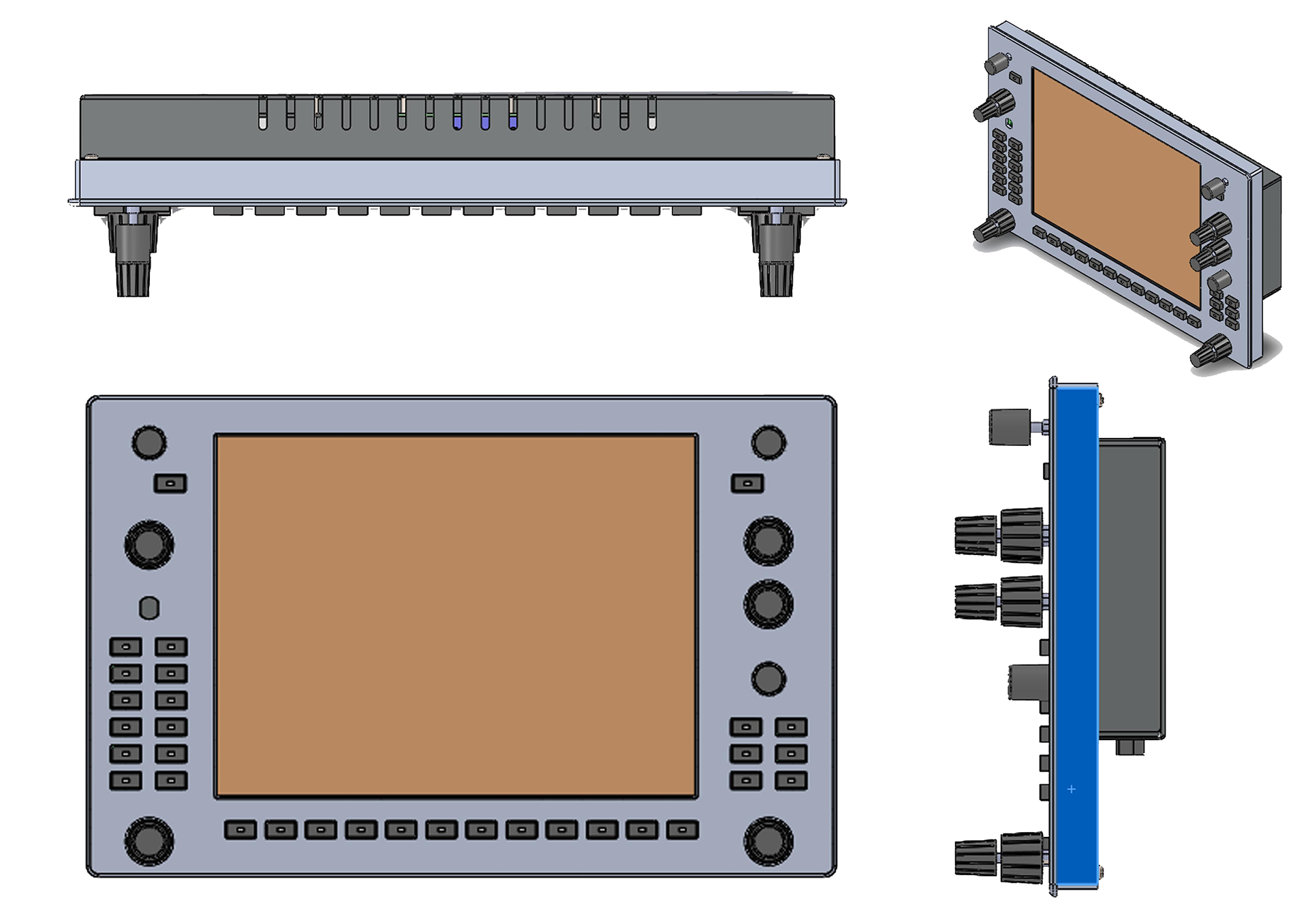
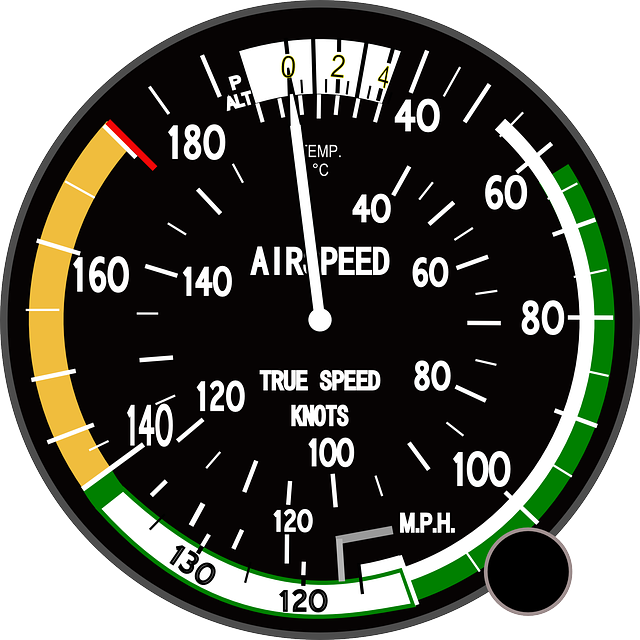


CAD model, the render of the CAD model and the final manufactured design.
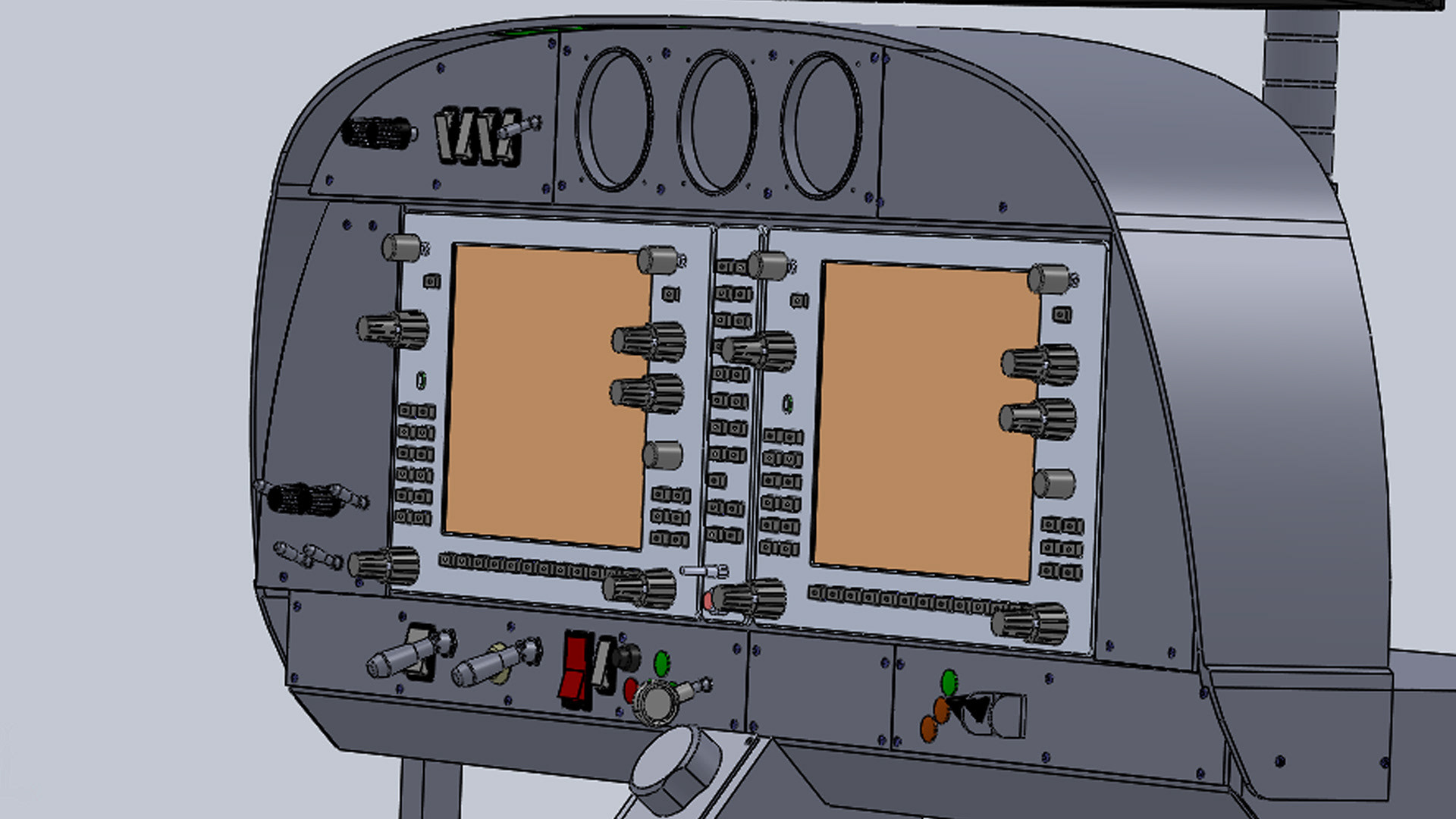
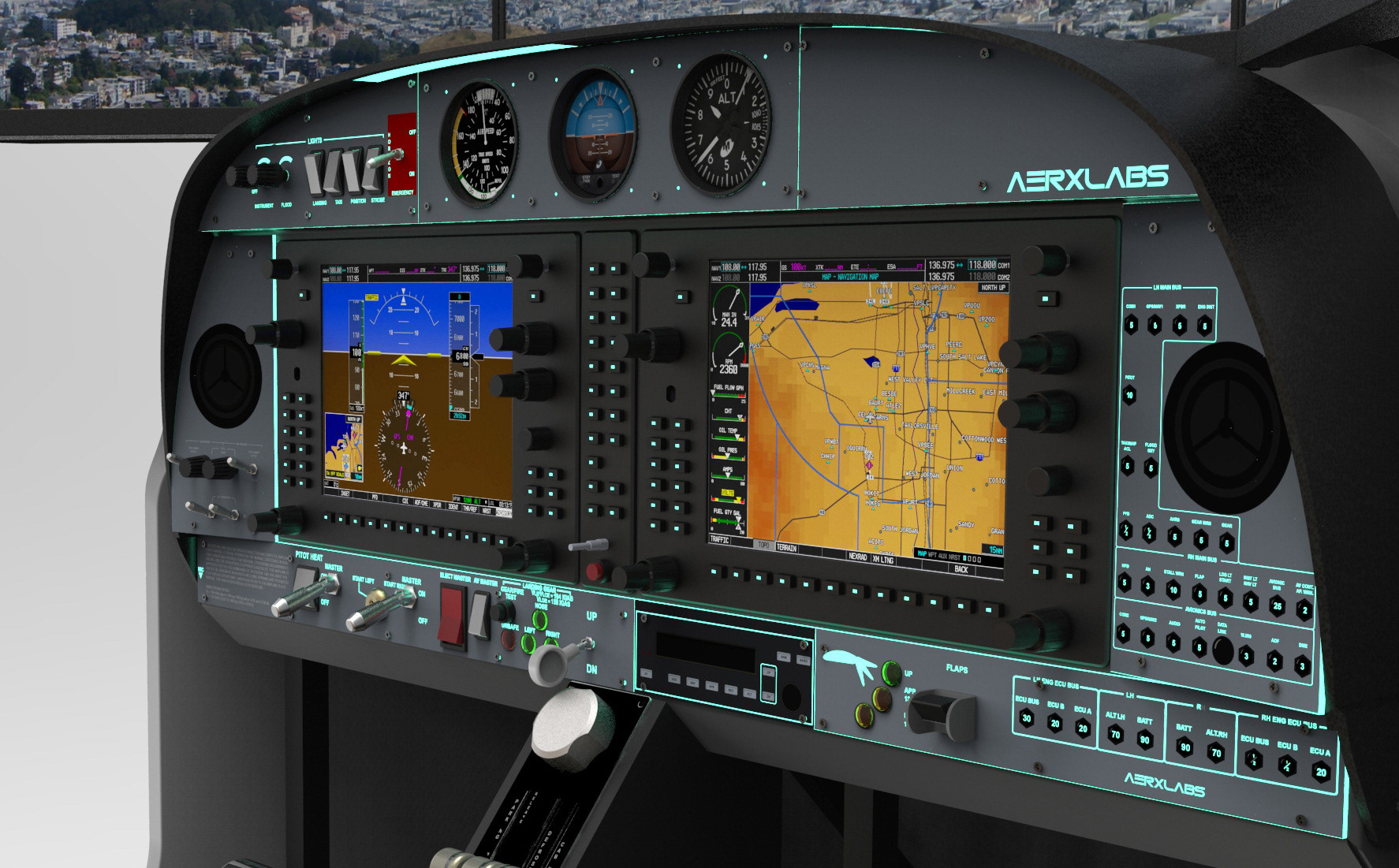
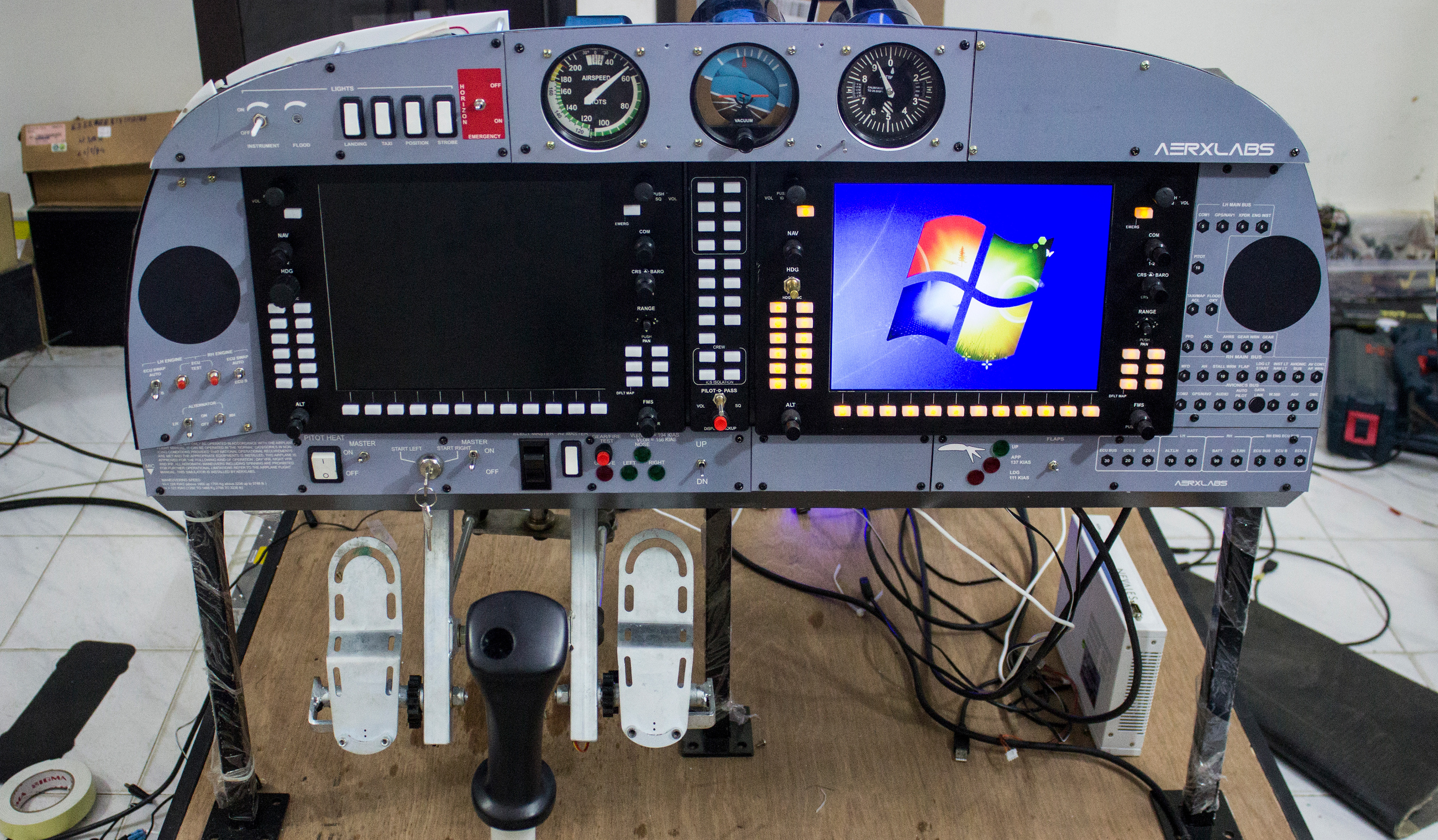
The Pedestal
The Pedestal is another important component of the aircraft. It controls all the major Engine related functions such as Throttle, Fuel Control and other things such as Parking Brake, Nose Trim, Rudder Trim, Defrost feature and Cabin Heat. It is located centrally between the Pilot and the Co-Pilot so that it can be used by both of them.

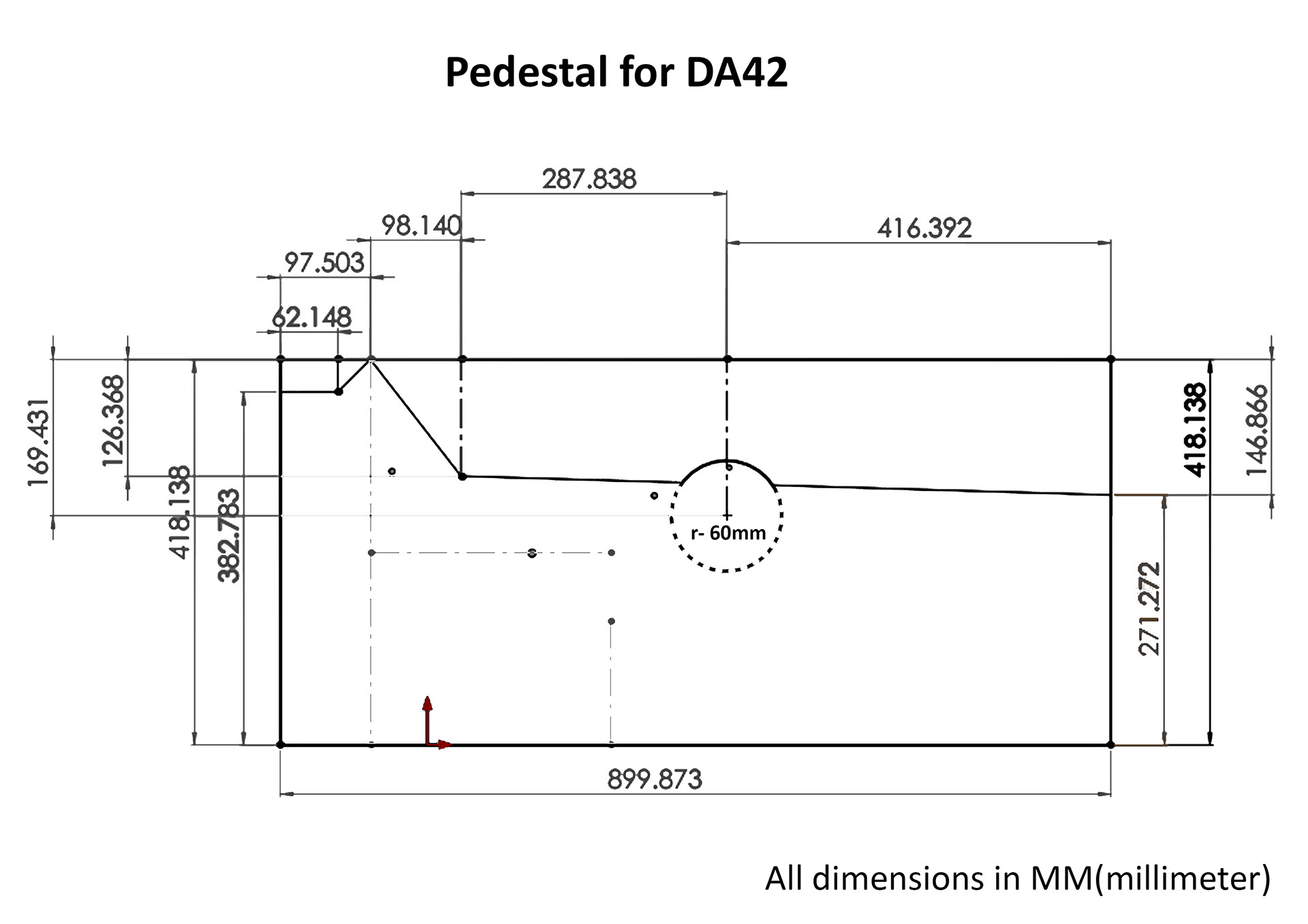


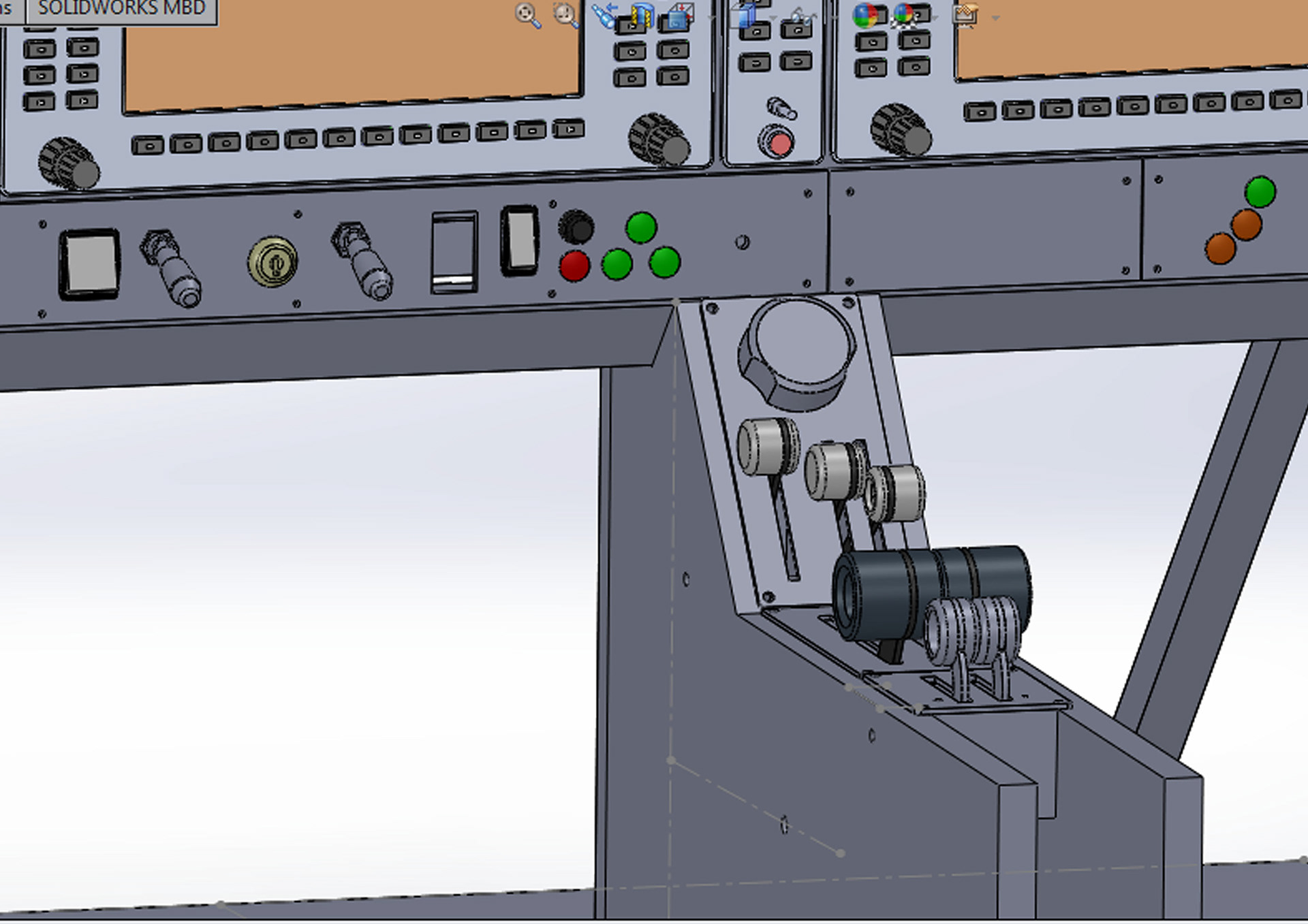
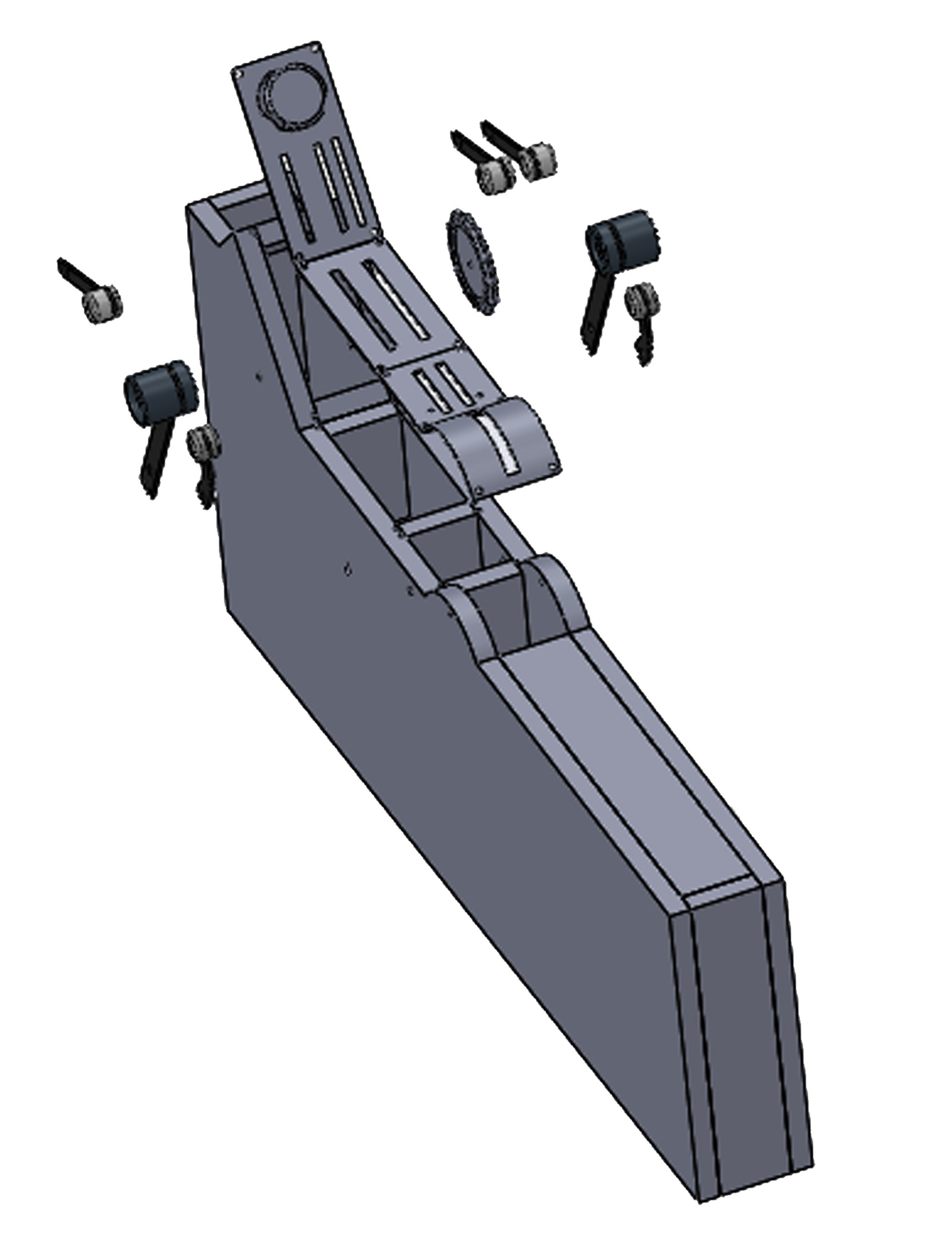



The first iteration of the Pedestal.
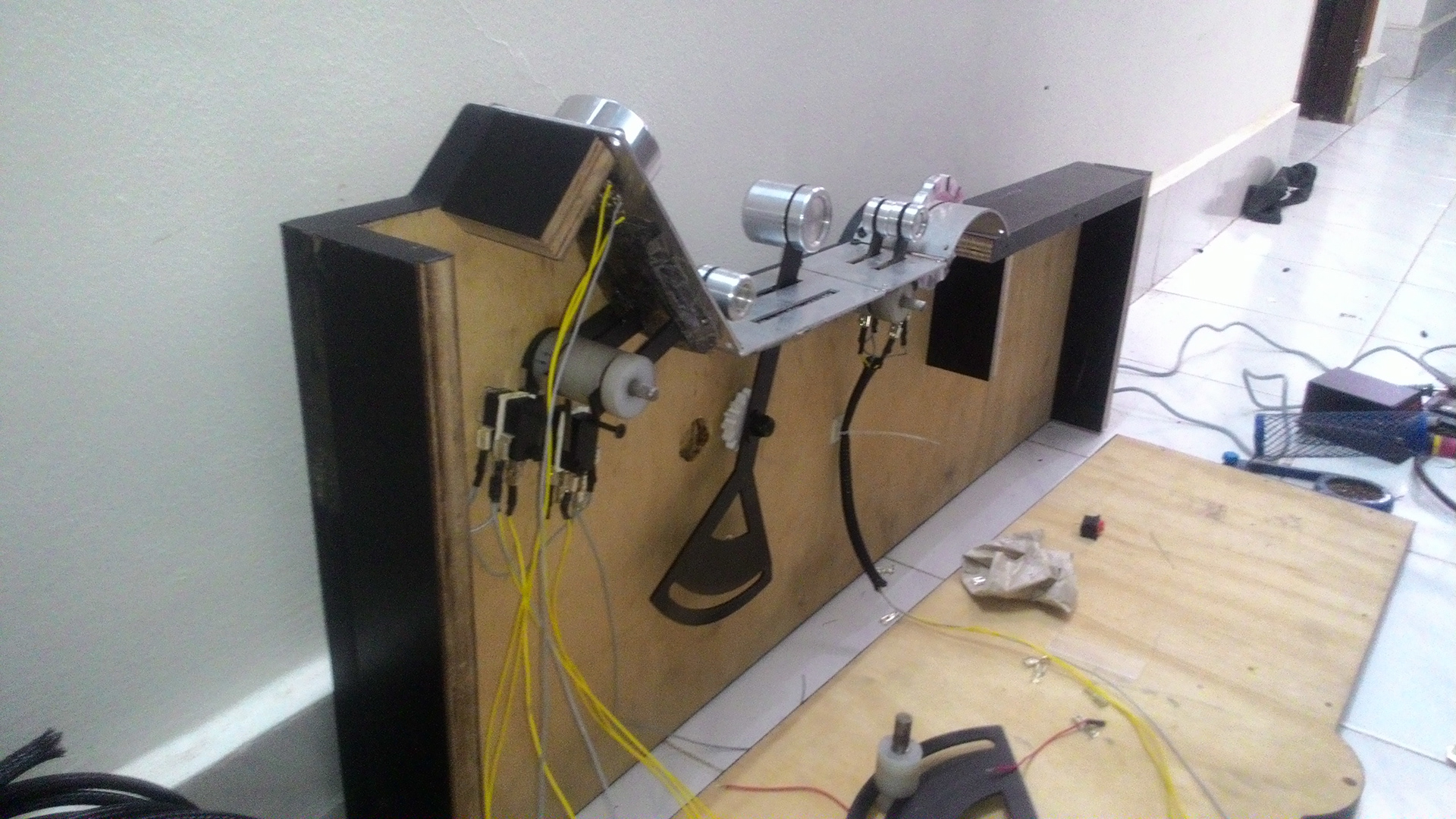
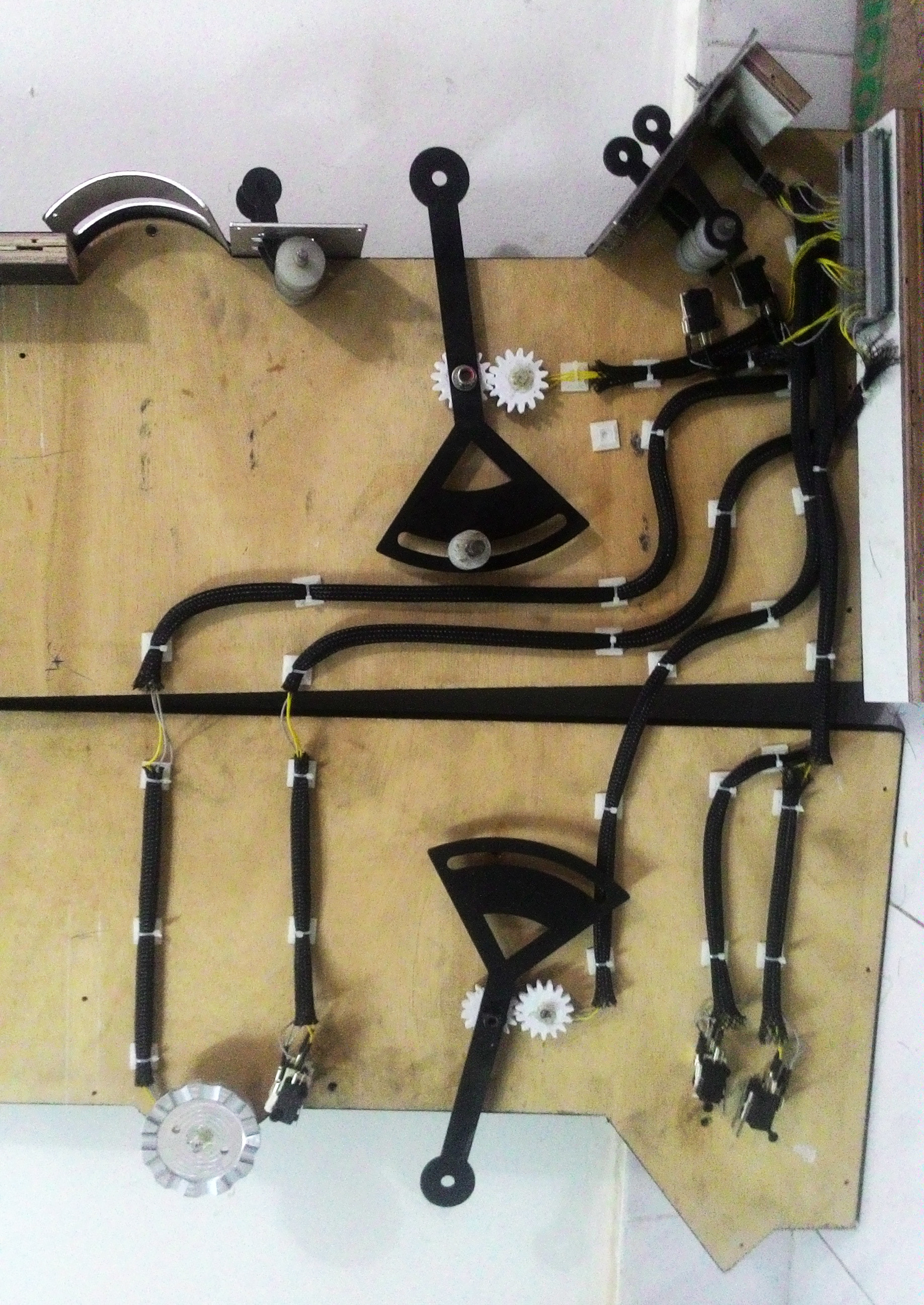
Version 2 of the pedestal for easier maintenance.
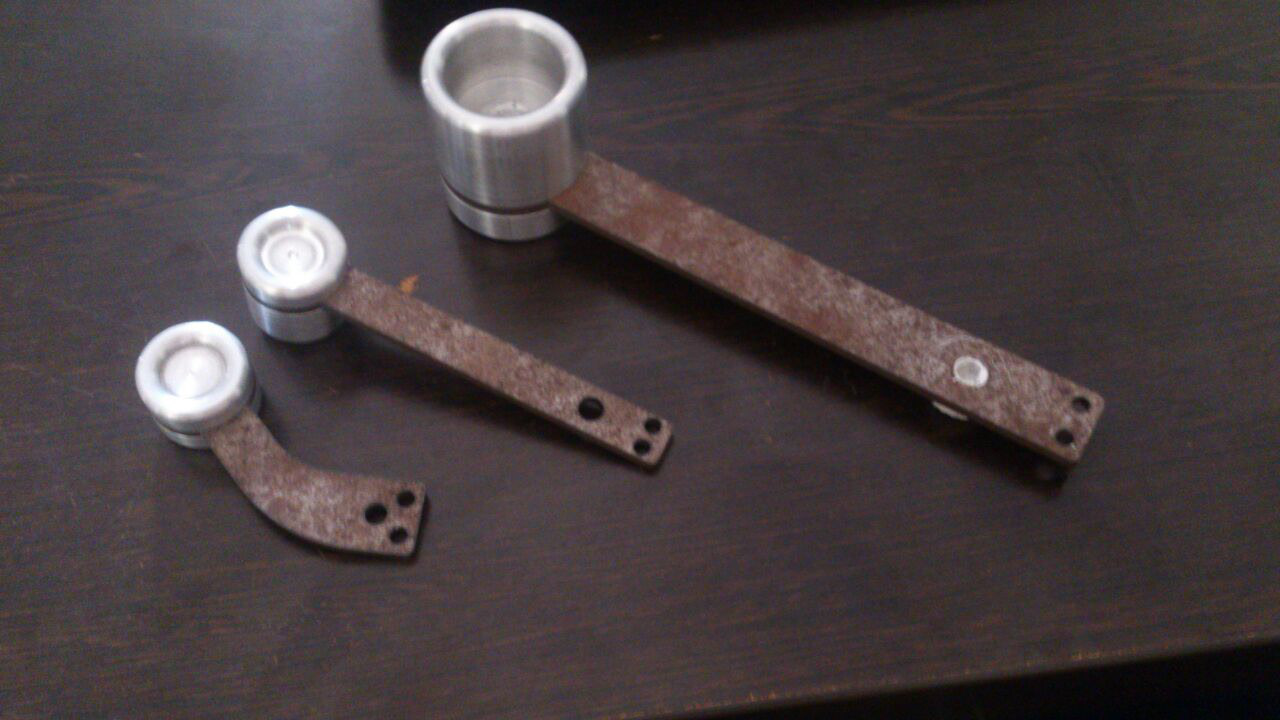

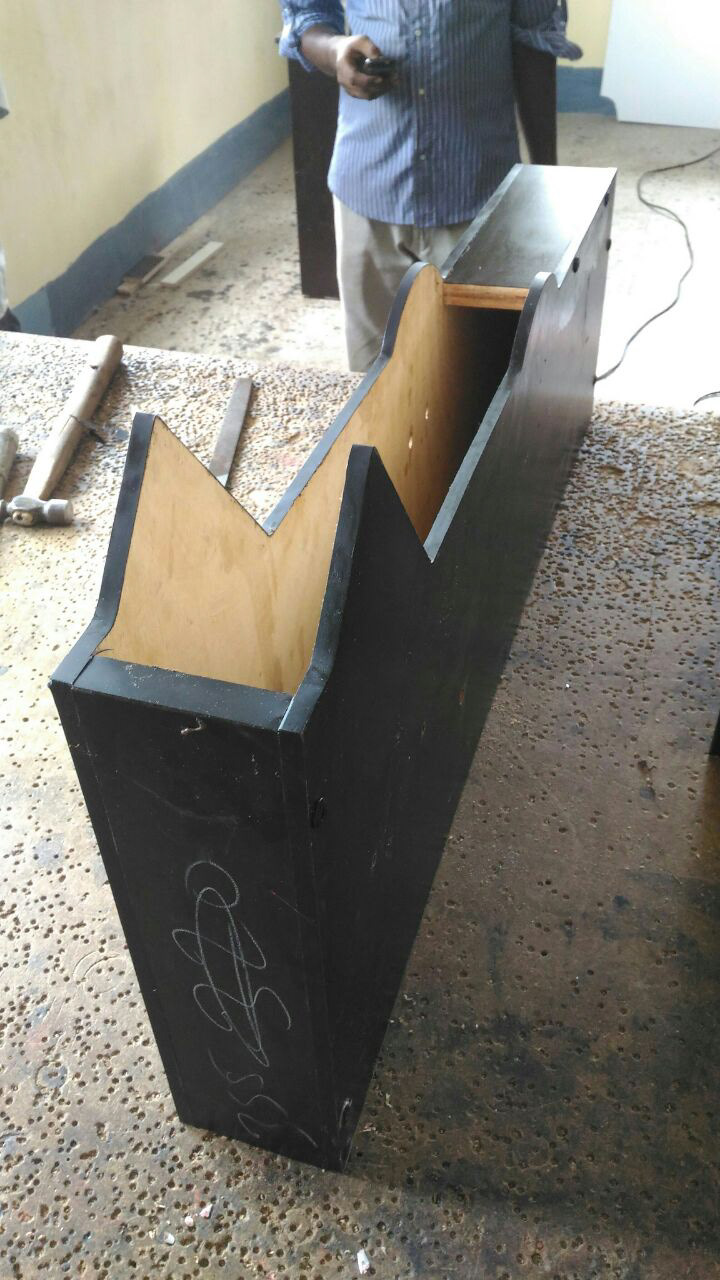
Version 3 of the pedestal - proposed concept.


Final pedestal installed in the simulator.

The cabinet designed for the Control Loading PCBs and the PSU. The modular design was fabricated using a 2mm aluminum sheet which was laser cut and then bent.

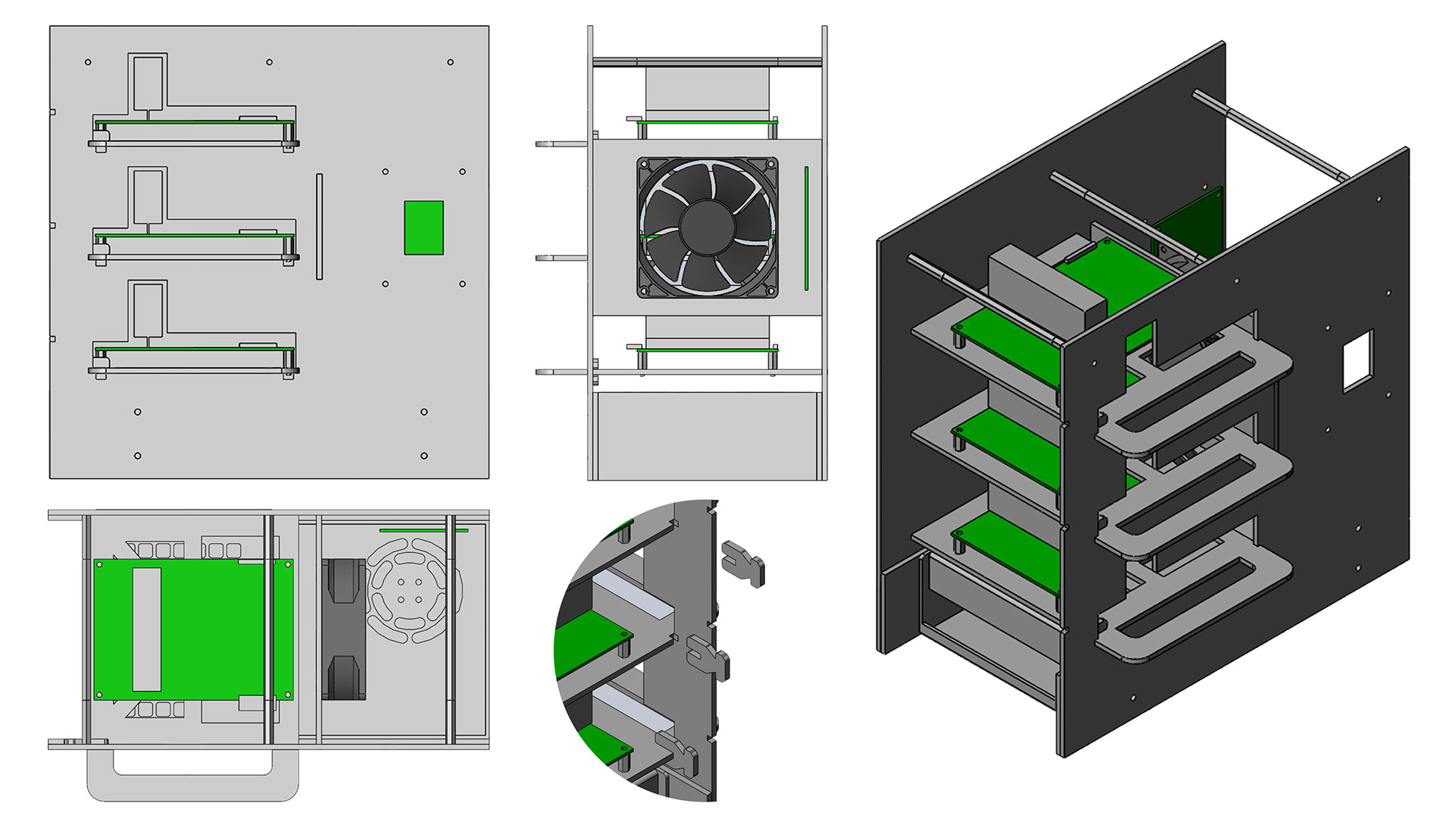
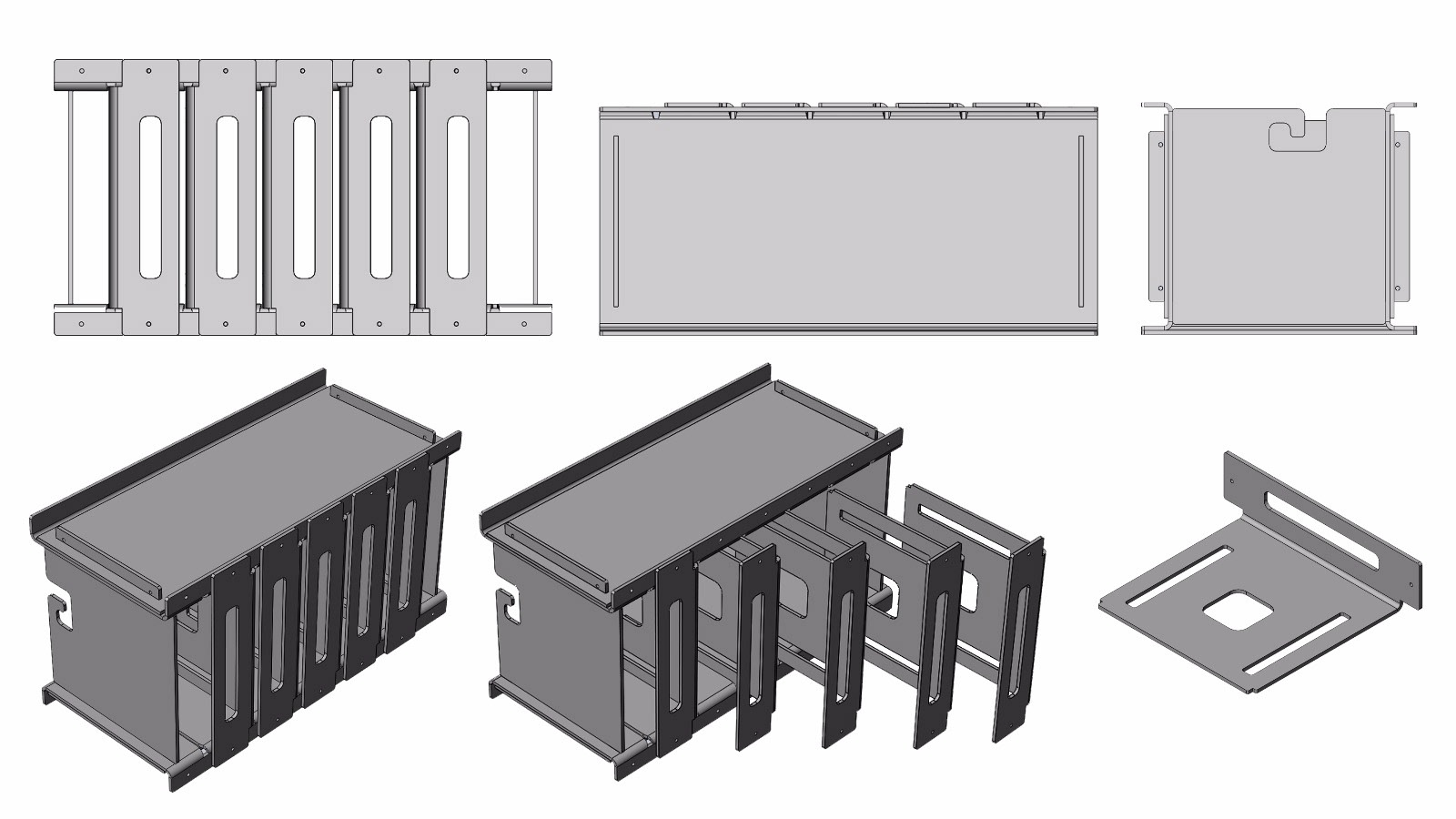
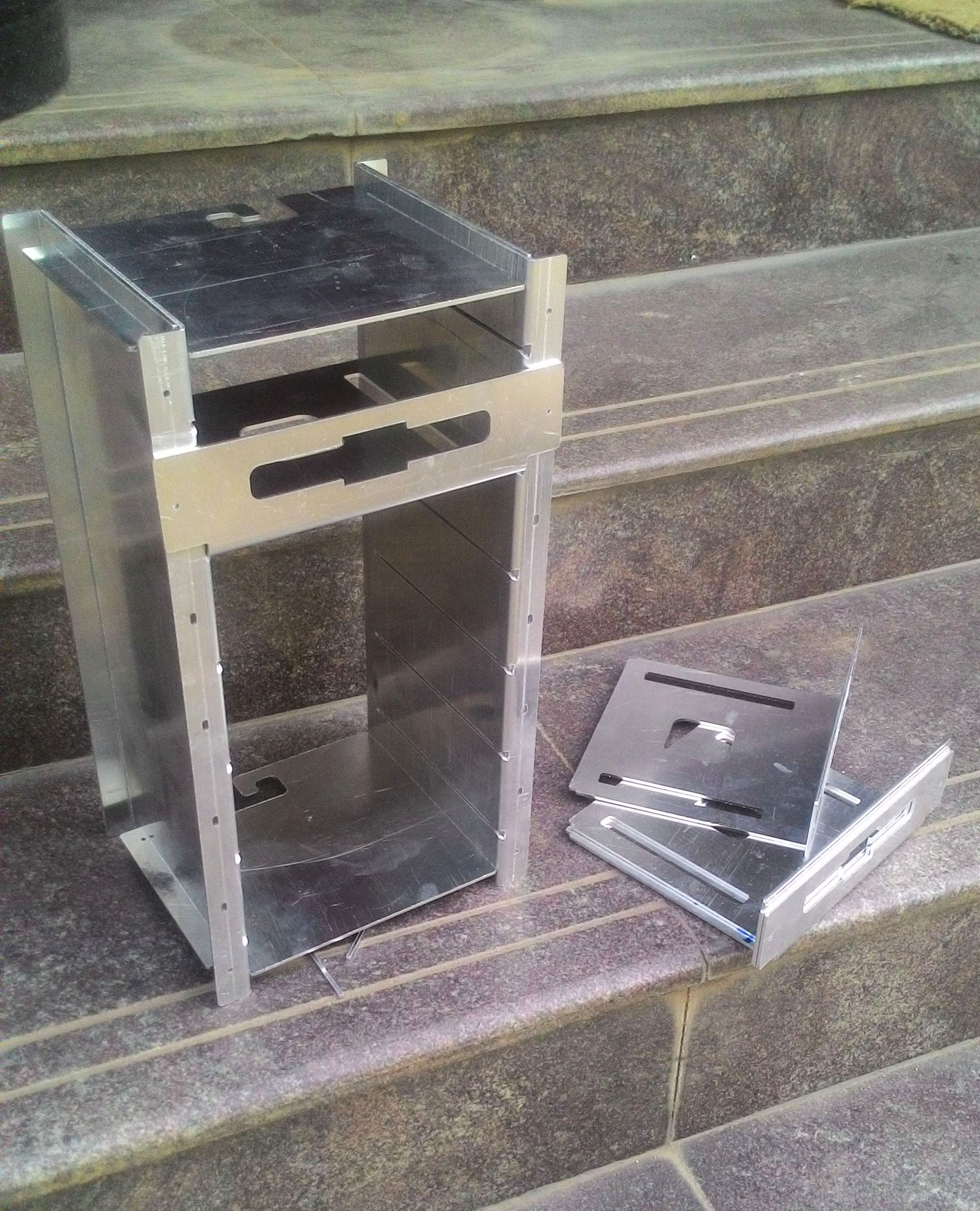
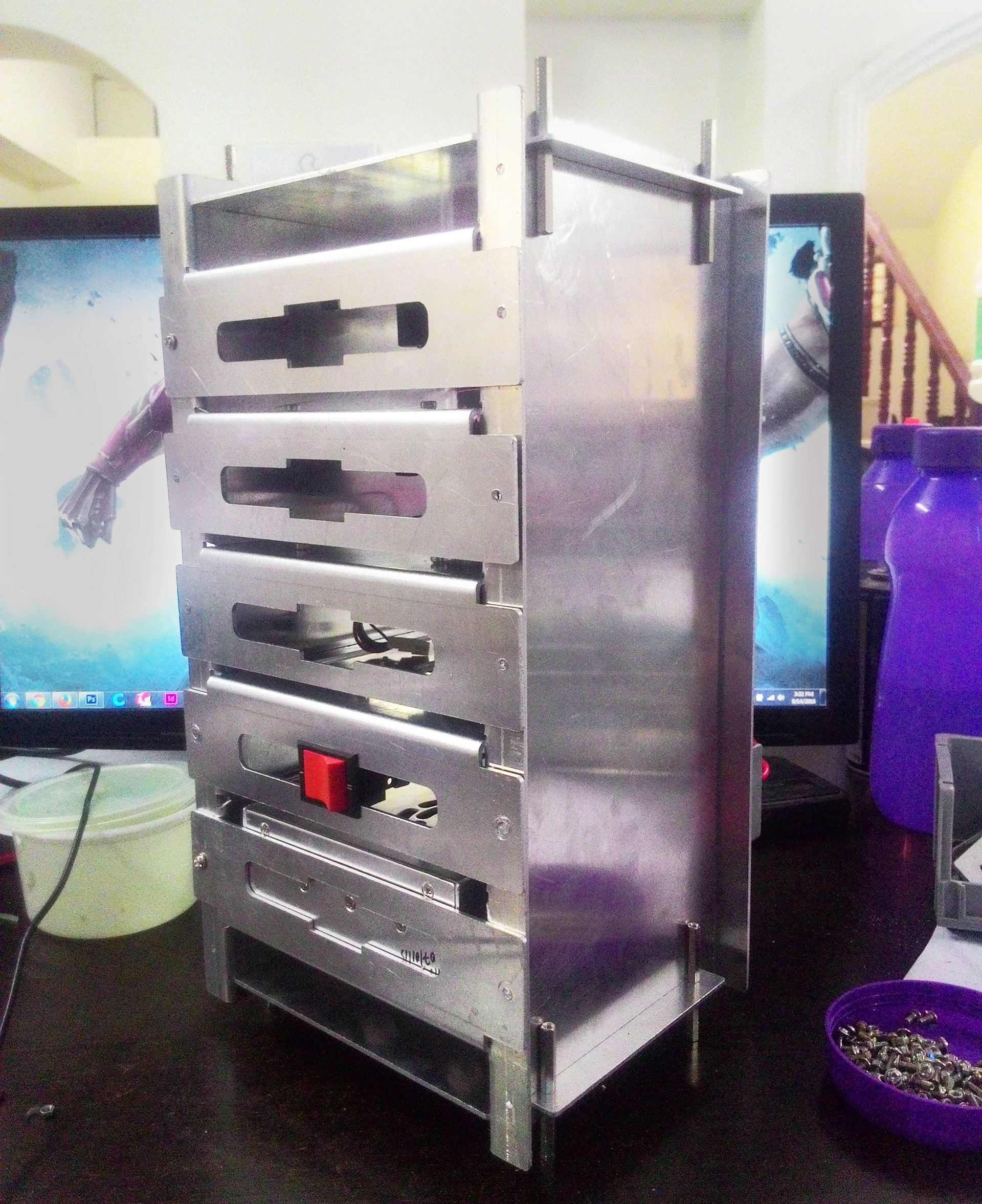
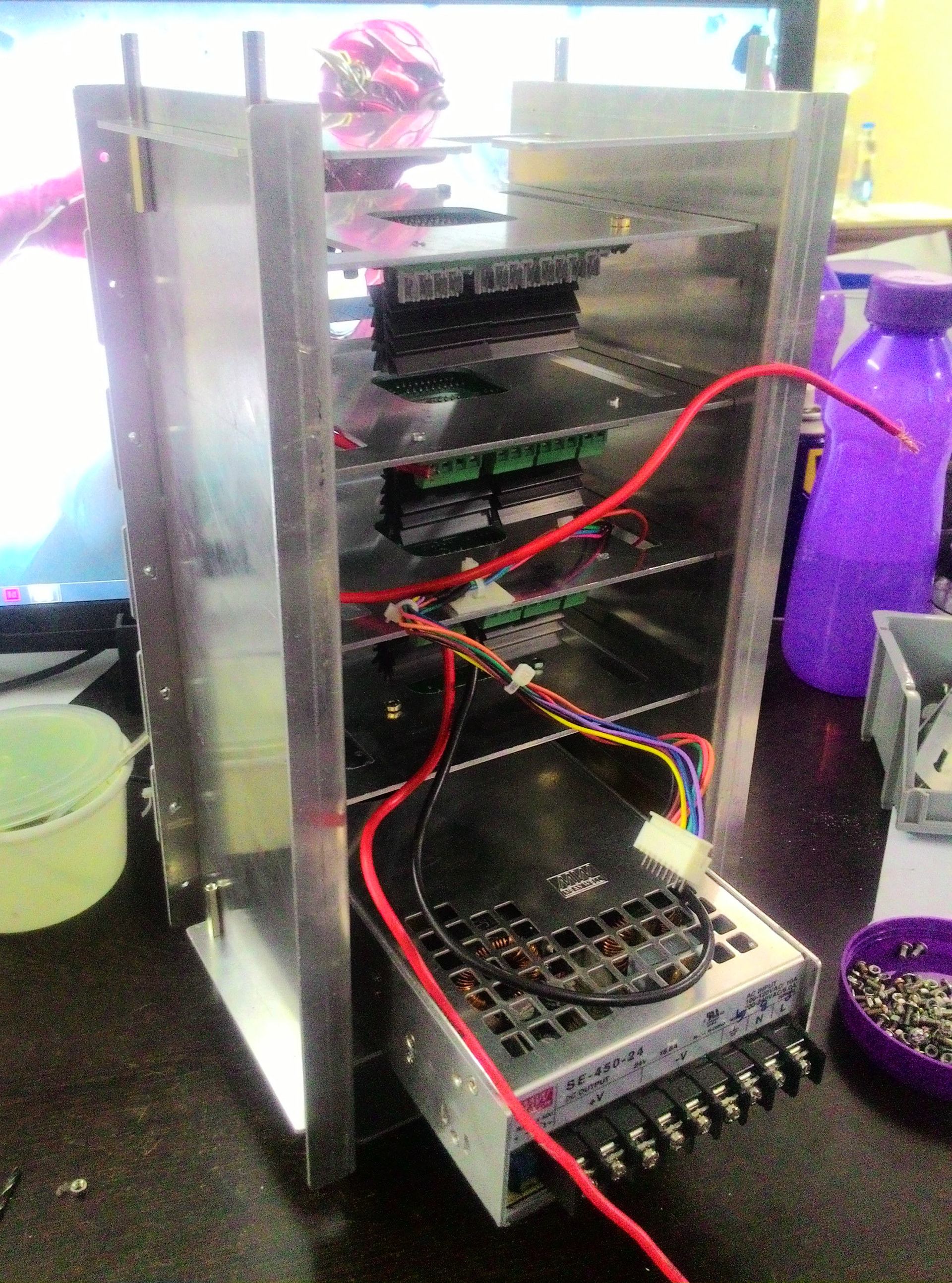
The basic Assembly of the Flight Simulator without the Shell.
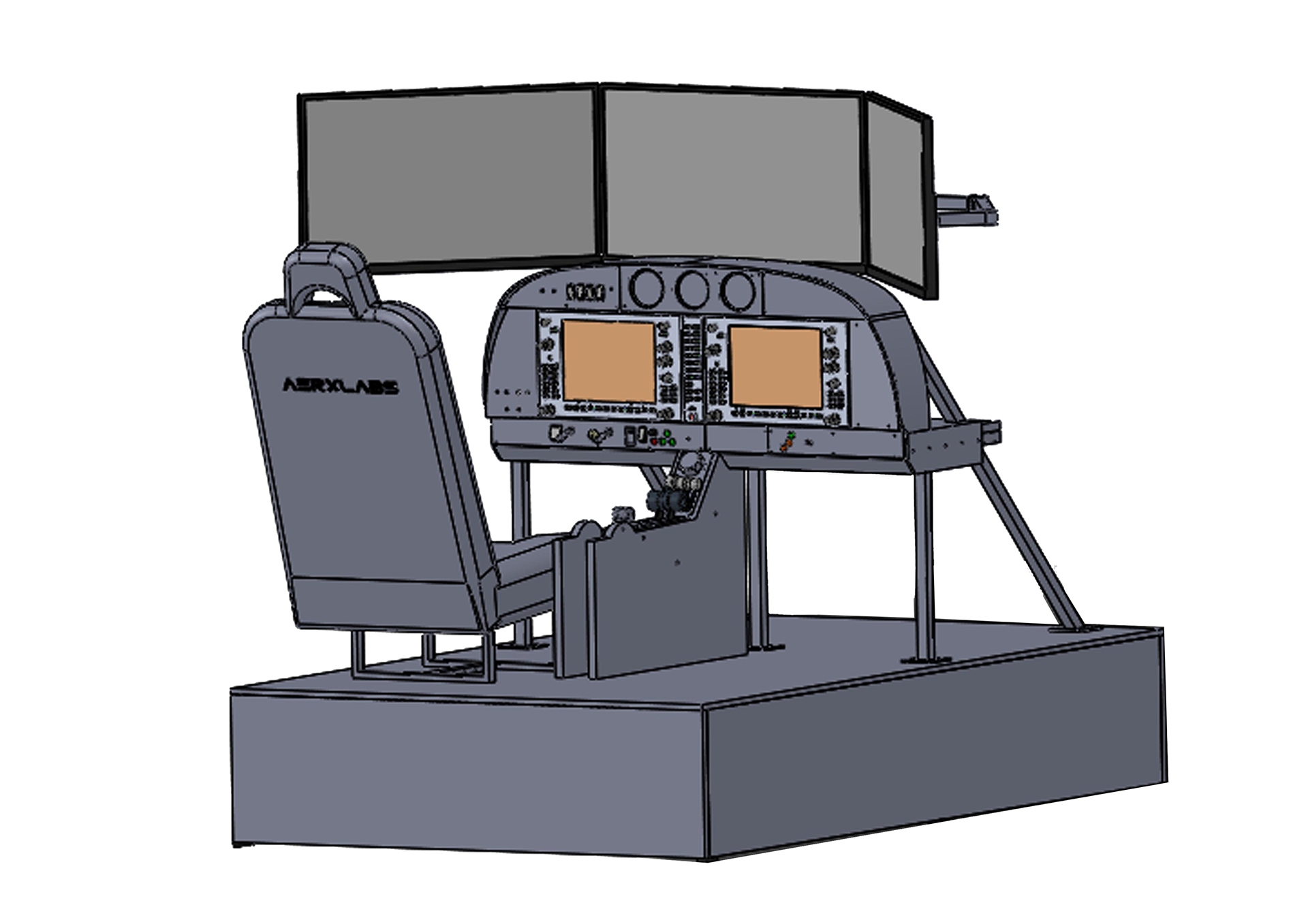
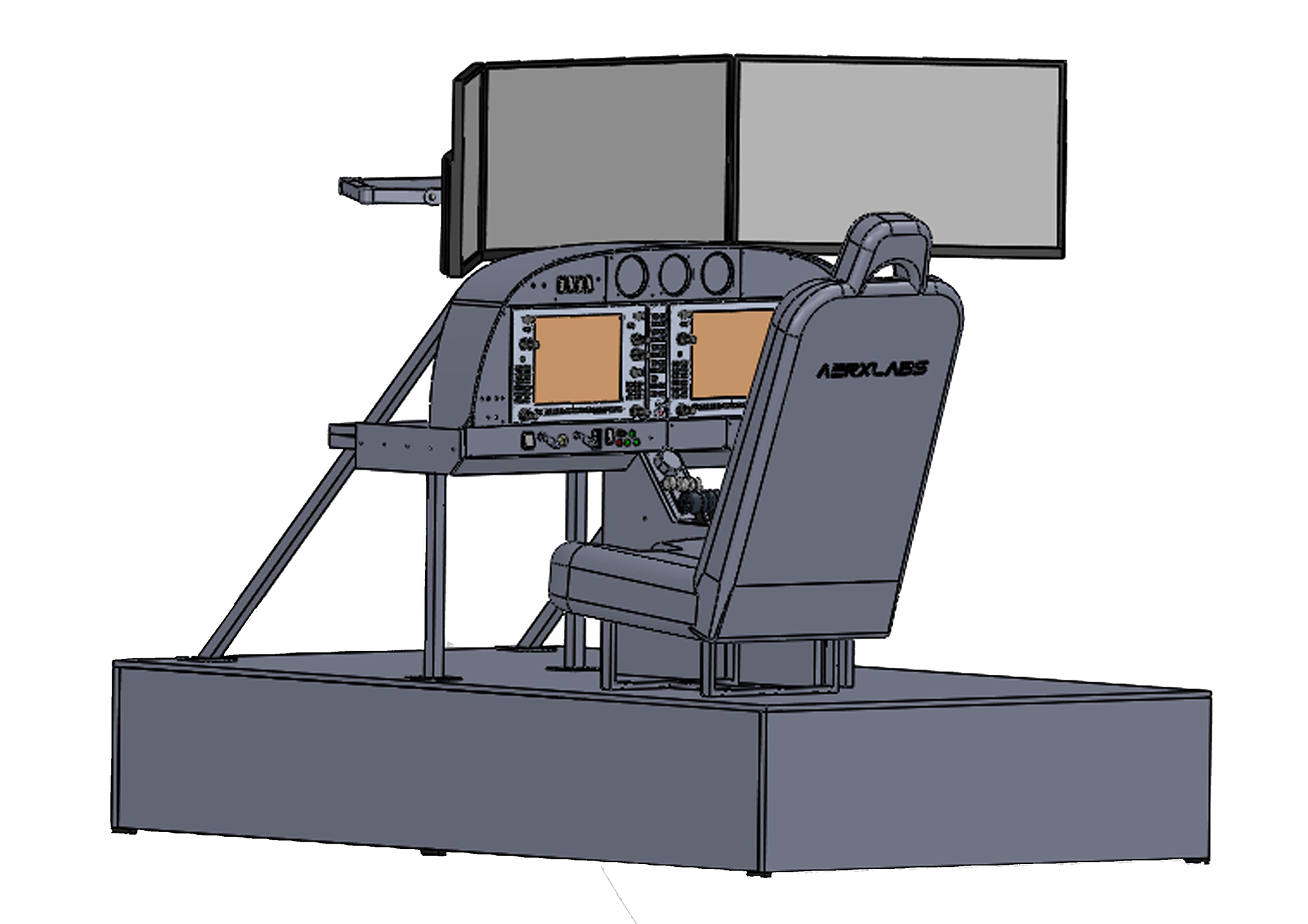

Explorations of the Shell for the Simulator.

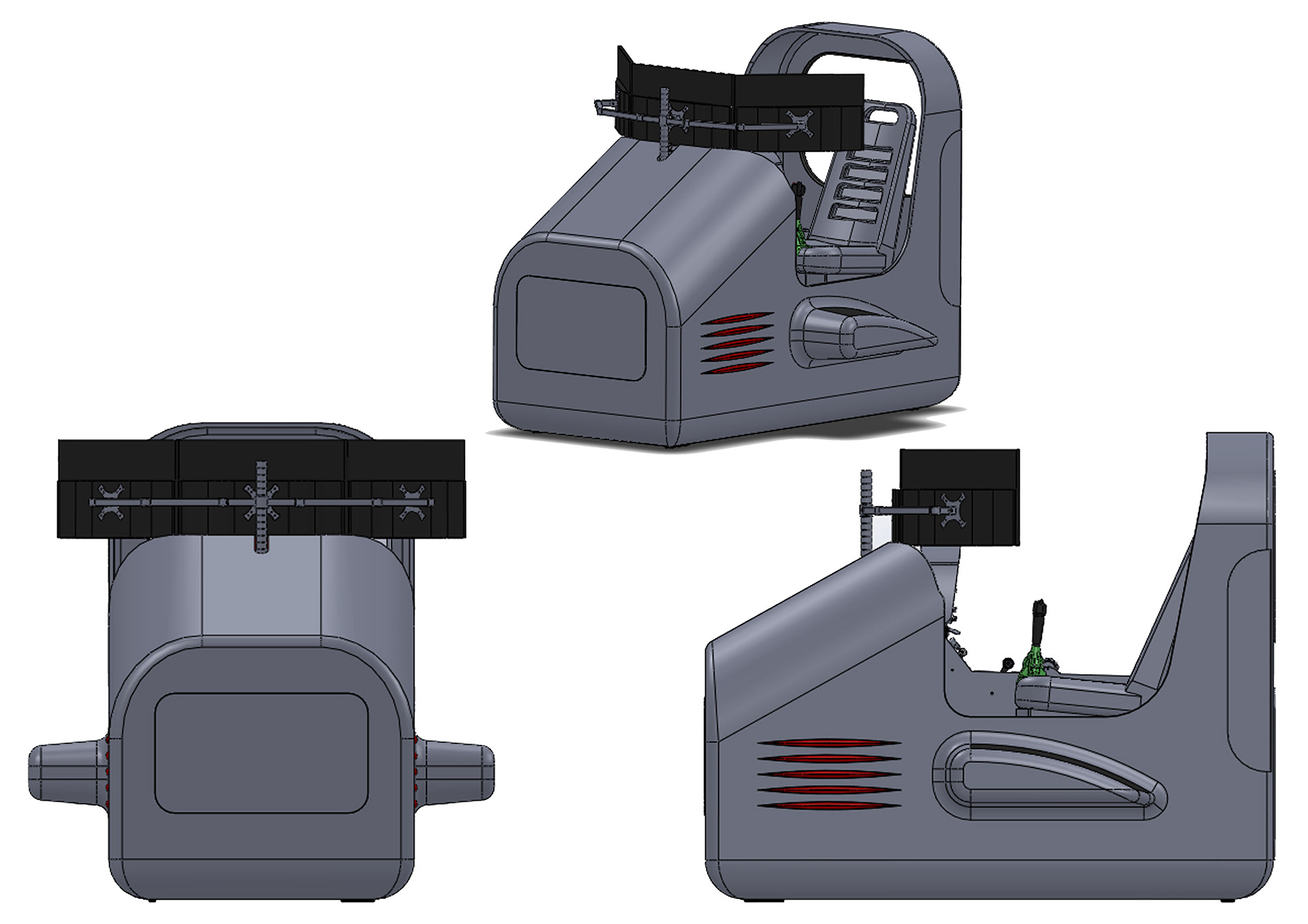
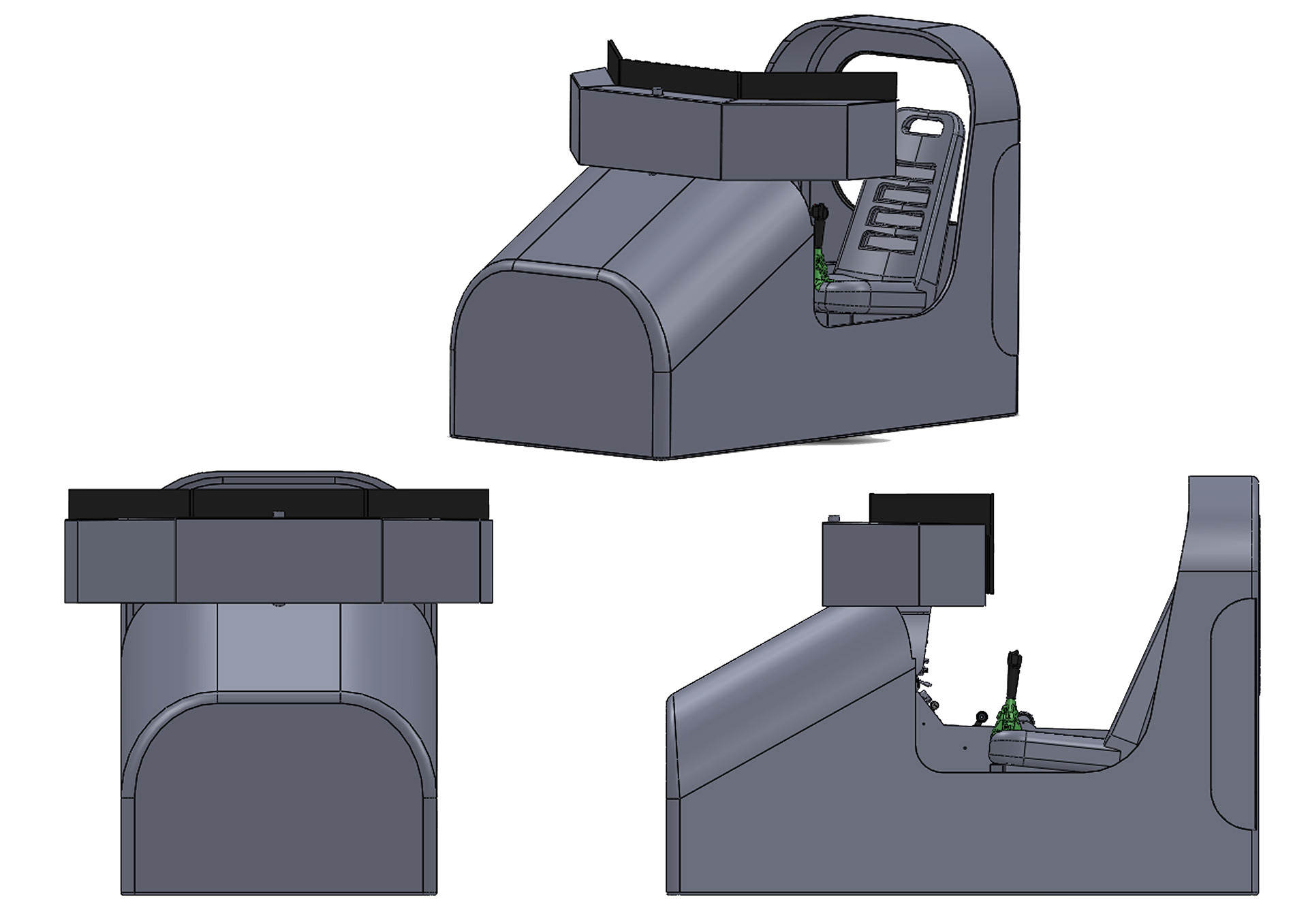

Concept Renders
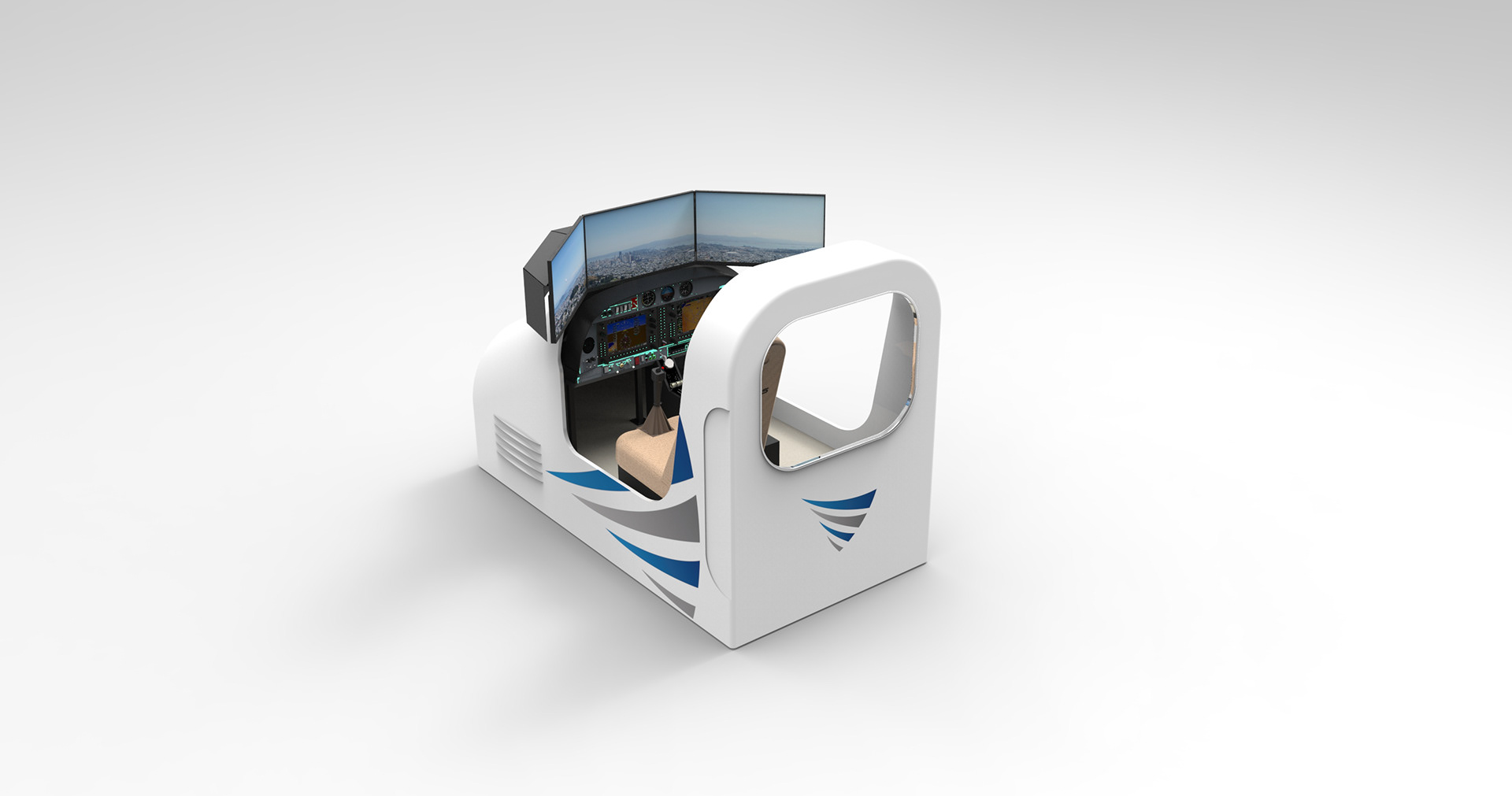

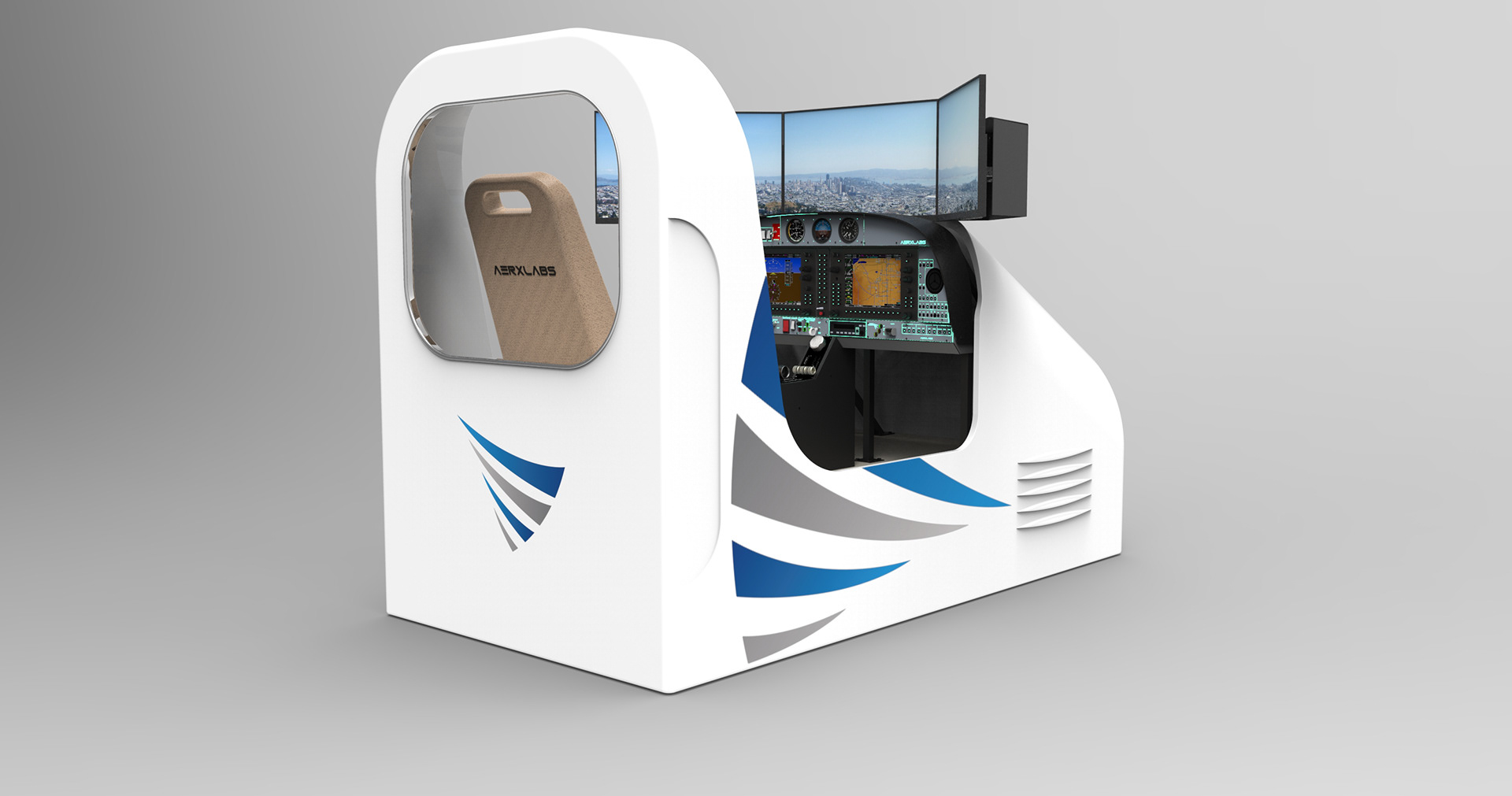

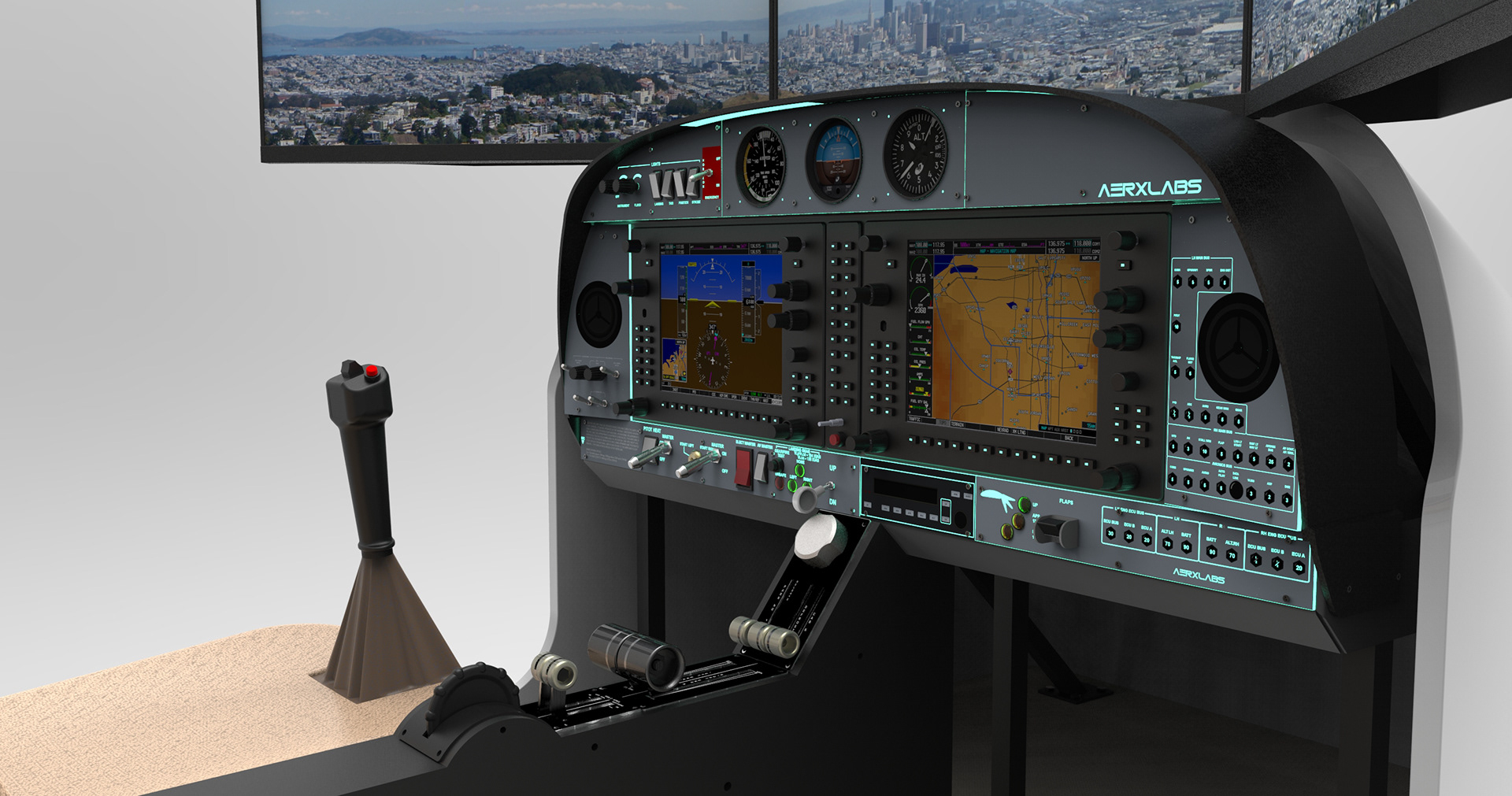

Renders of the DA 42 Flight Simulator without the shell.
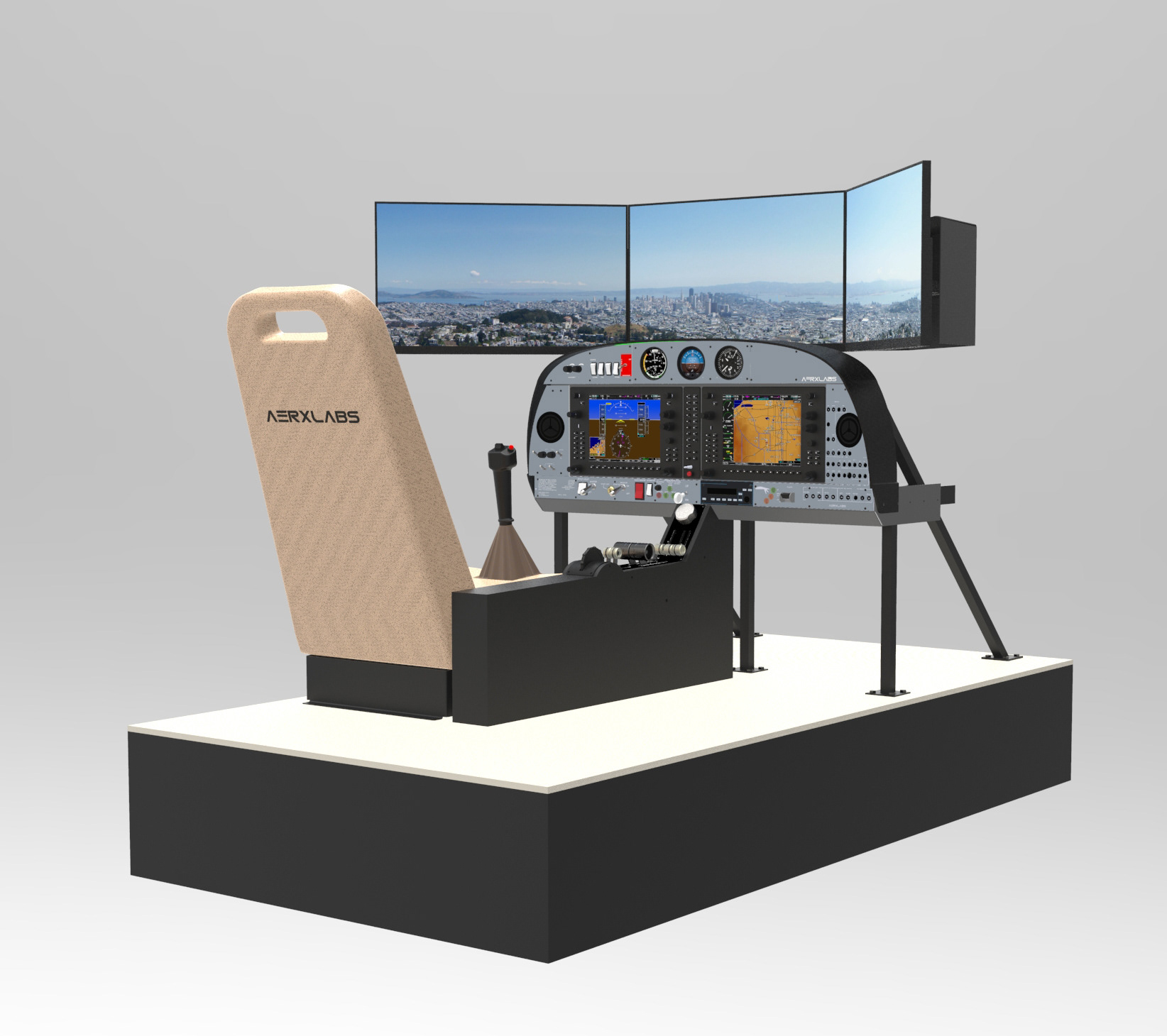

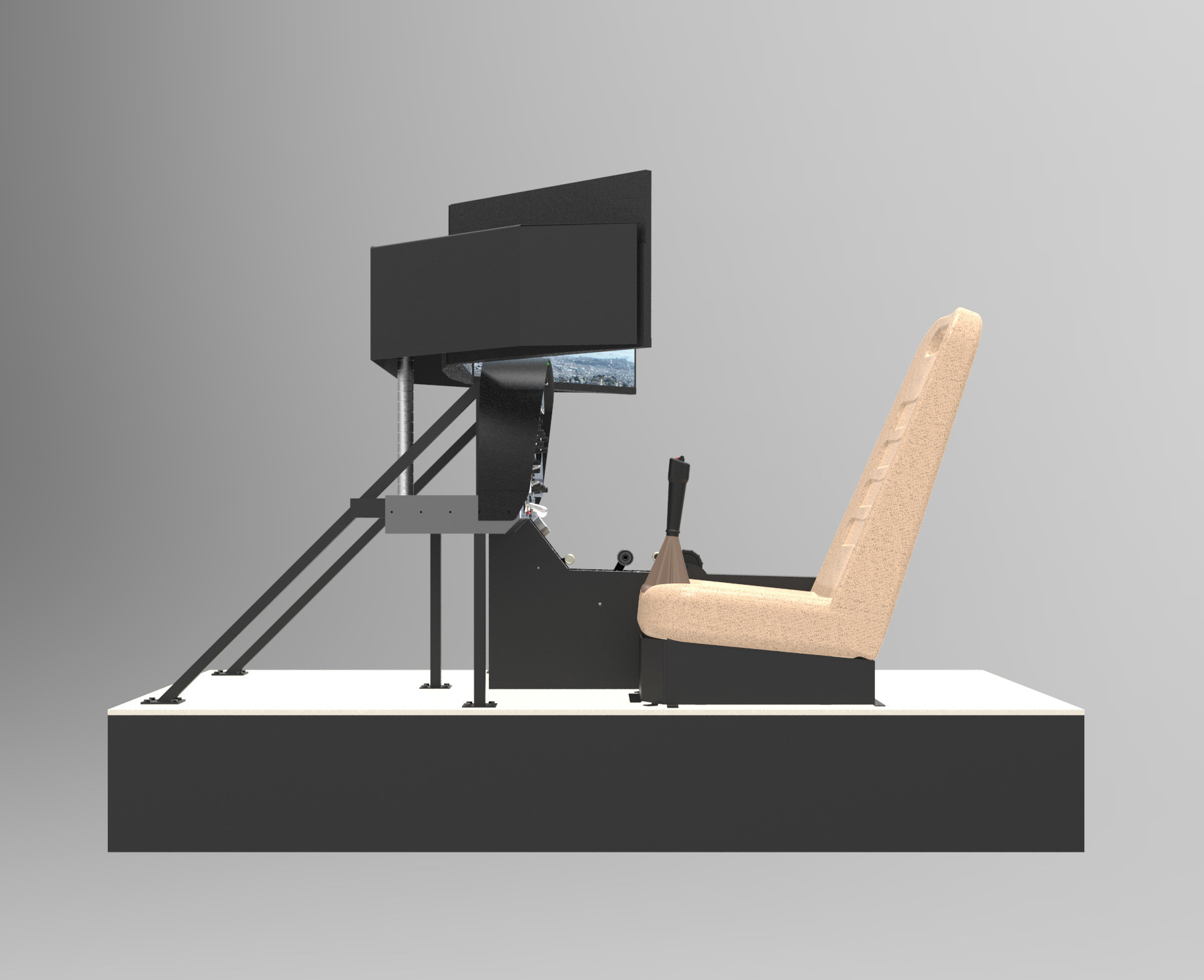
Flight Simulator in the testing phase.
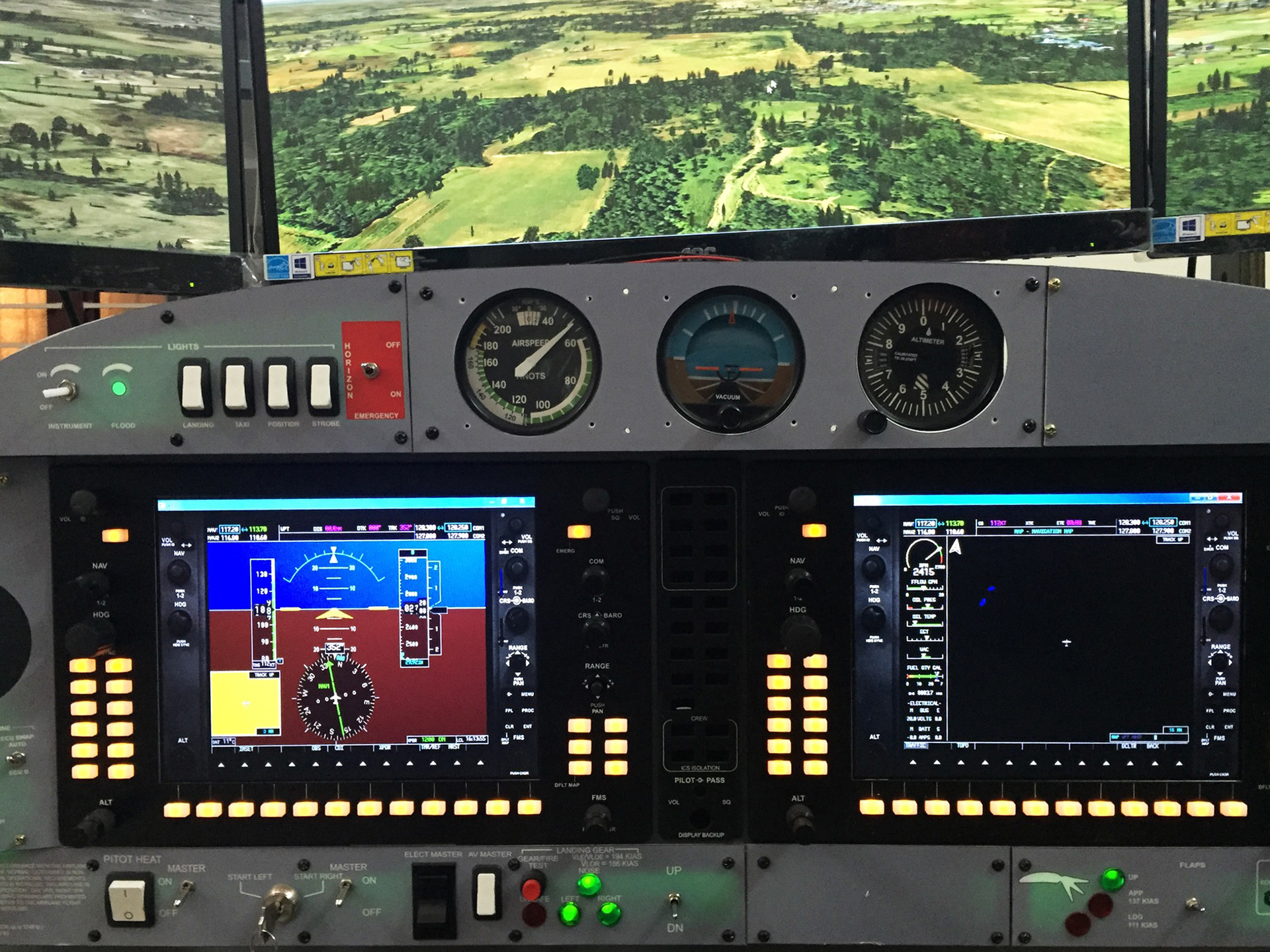
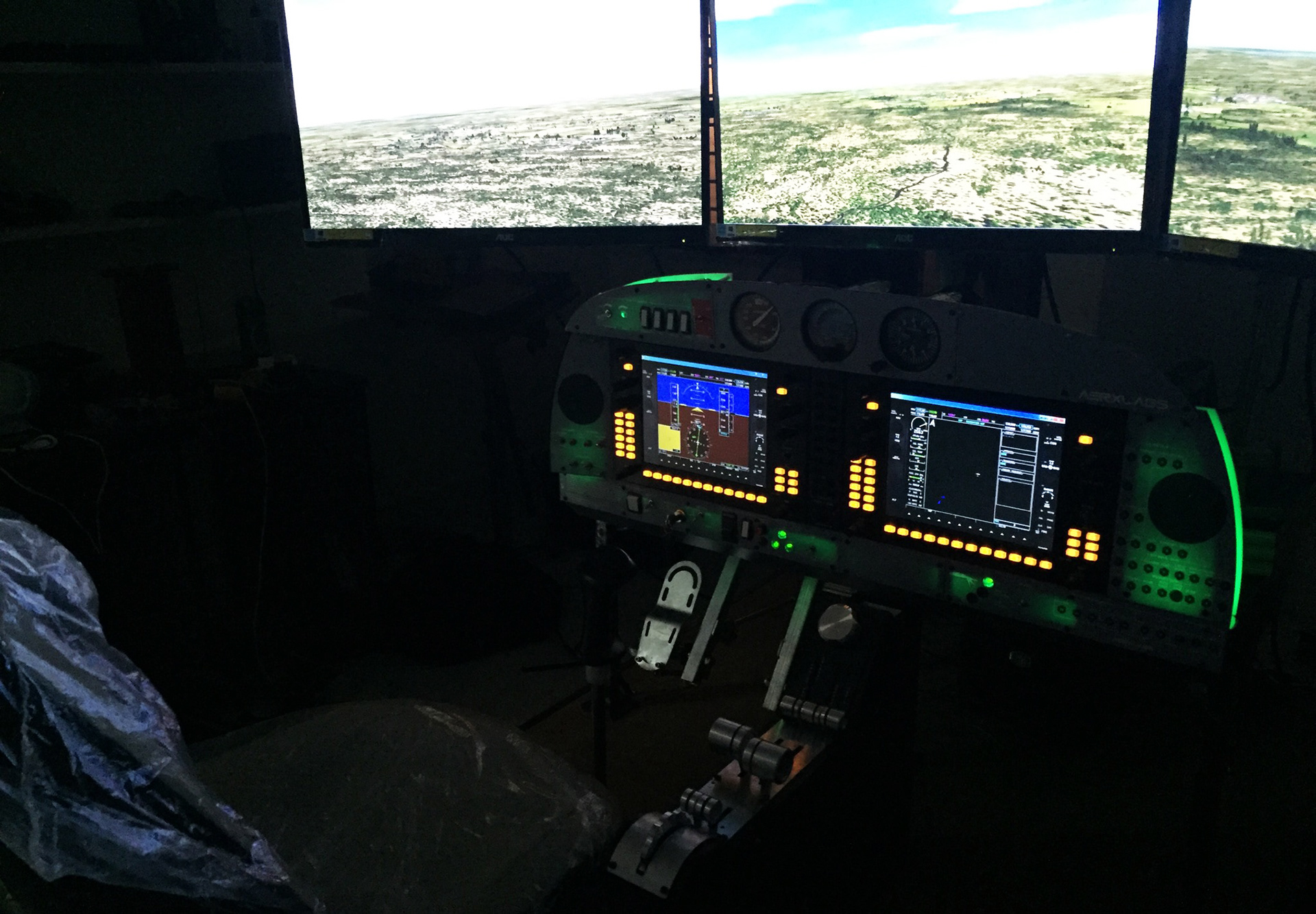

Final shell of the Flight Simulator.

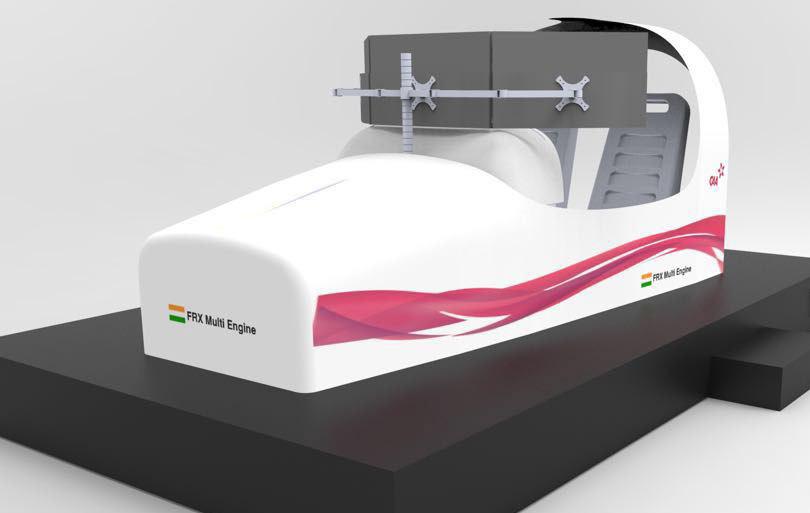
The shell getting fabricated at a workshop.



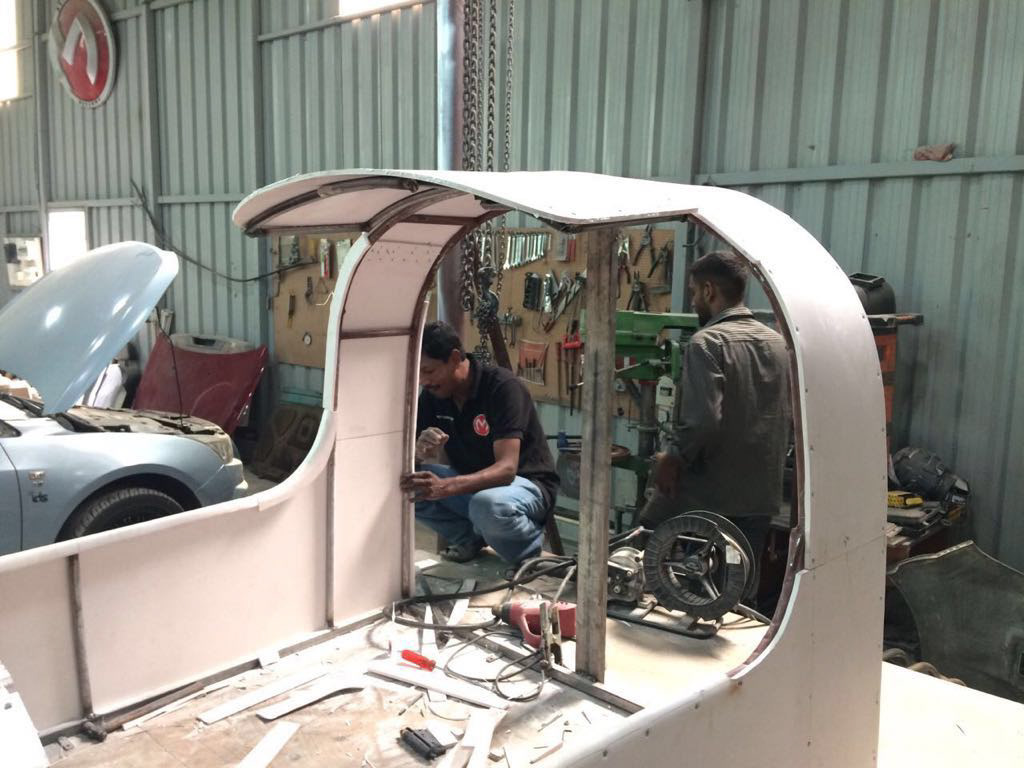
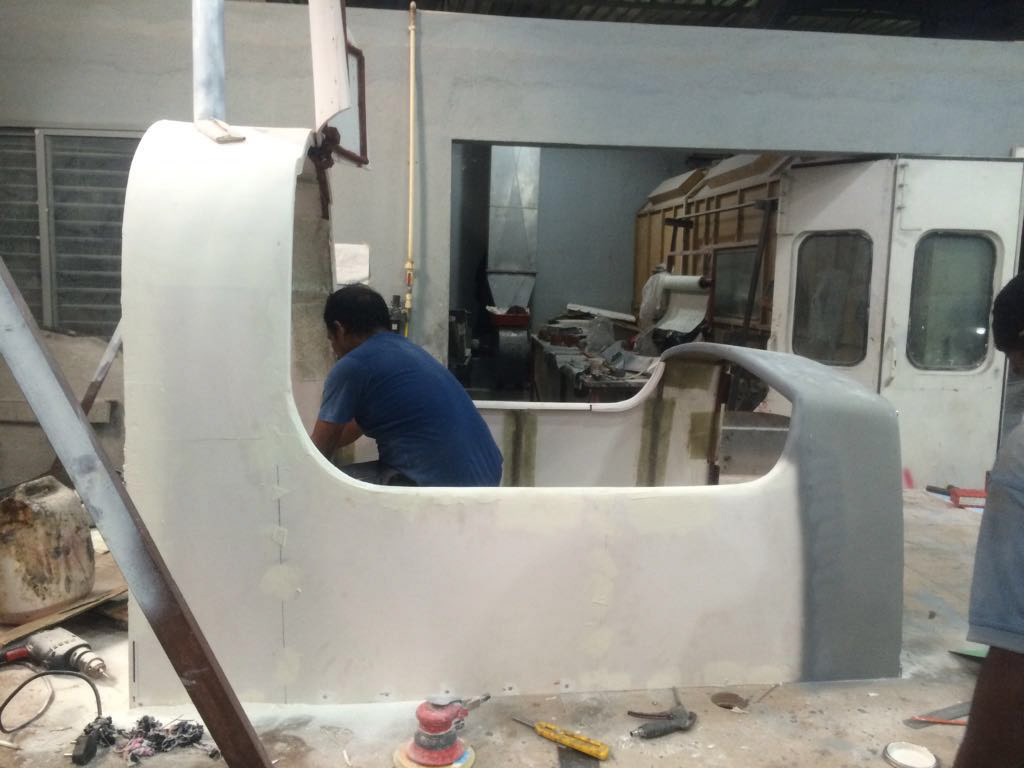
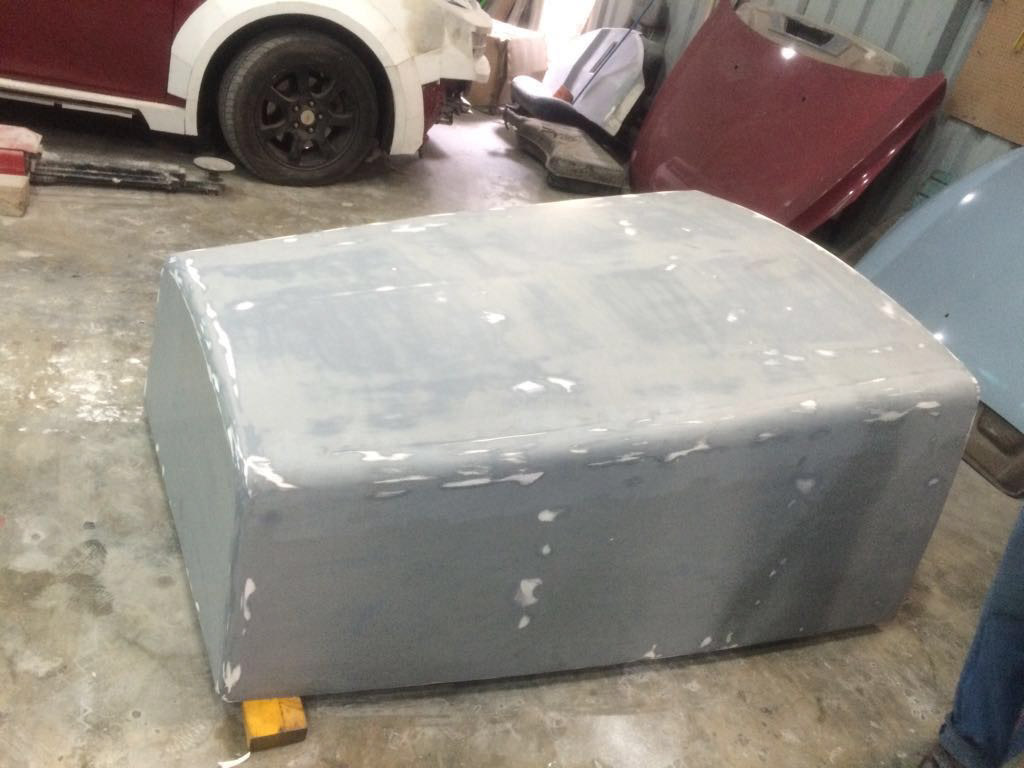
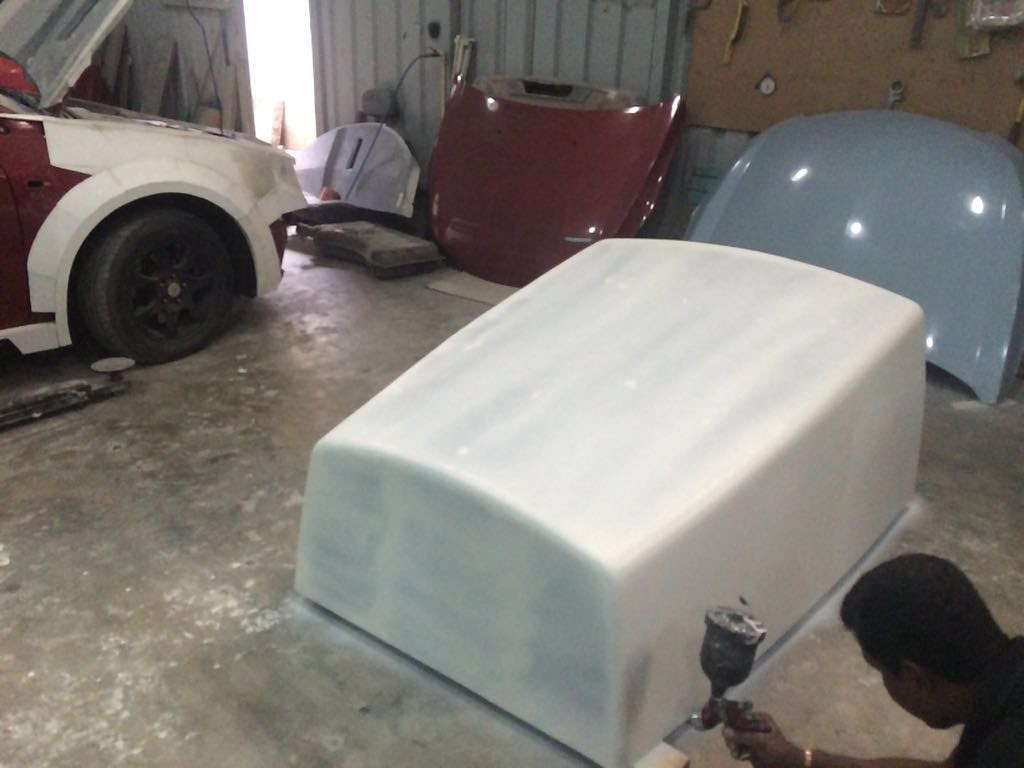

The shell with all the decals to make it appealing.
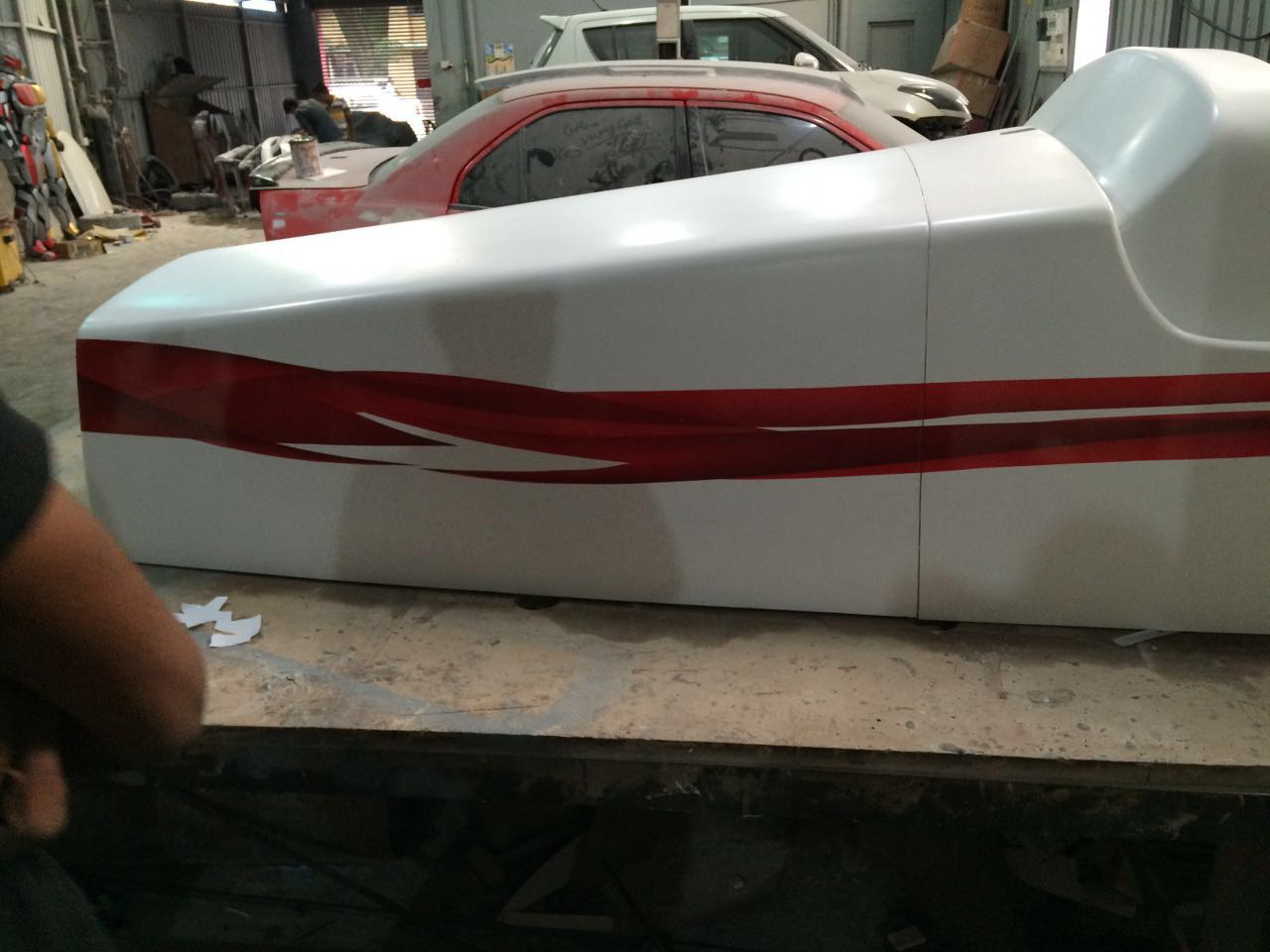
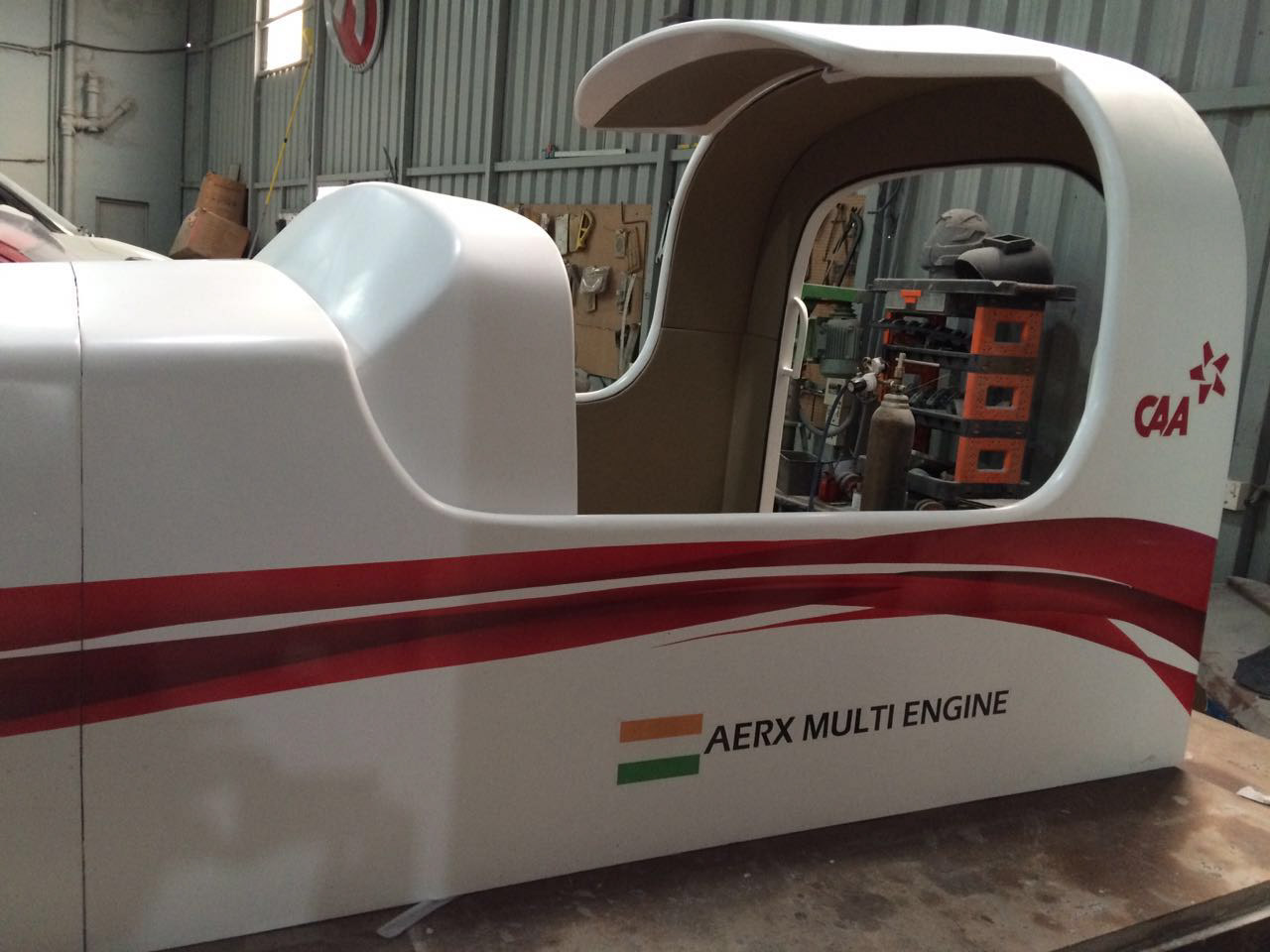

Due to the client requirement, we had to reduce the length of the shell at the last minute, which was done by me, inhouse. It consisted of cutting the shell, re-constructing the internal metal frame, welding and grinding and then using fiber glass and resin as reinforcement to the material used to close it down. Once this was done, it underwent finishing processes like sanding and painting to make it look new again.
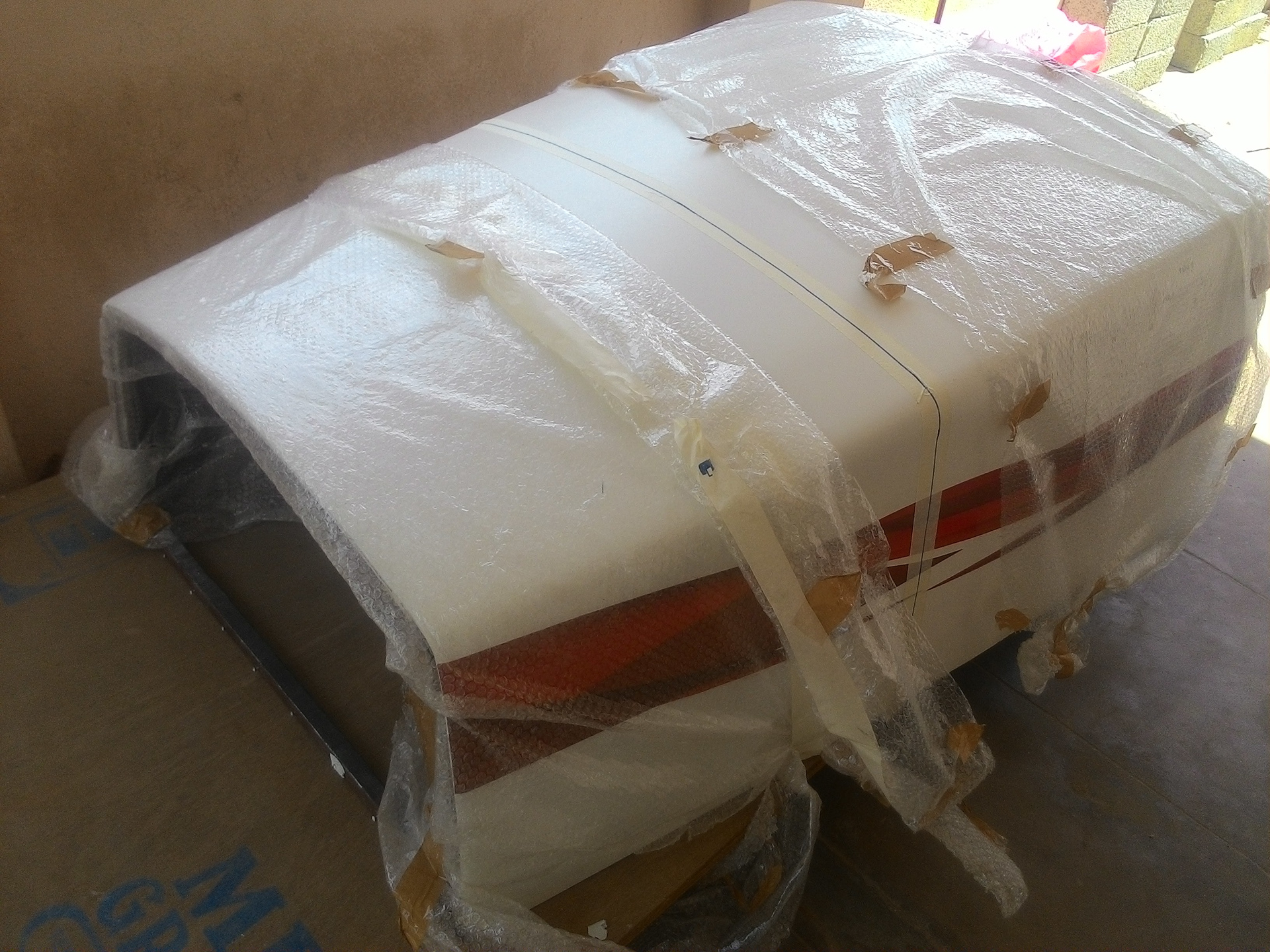
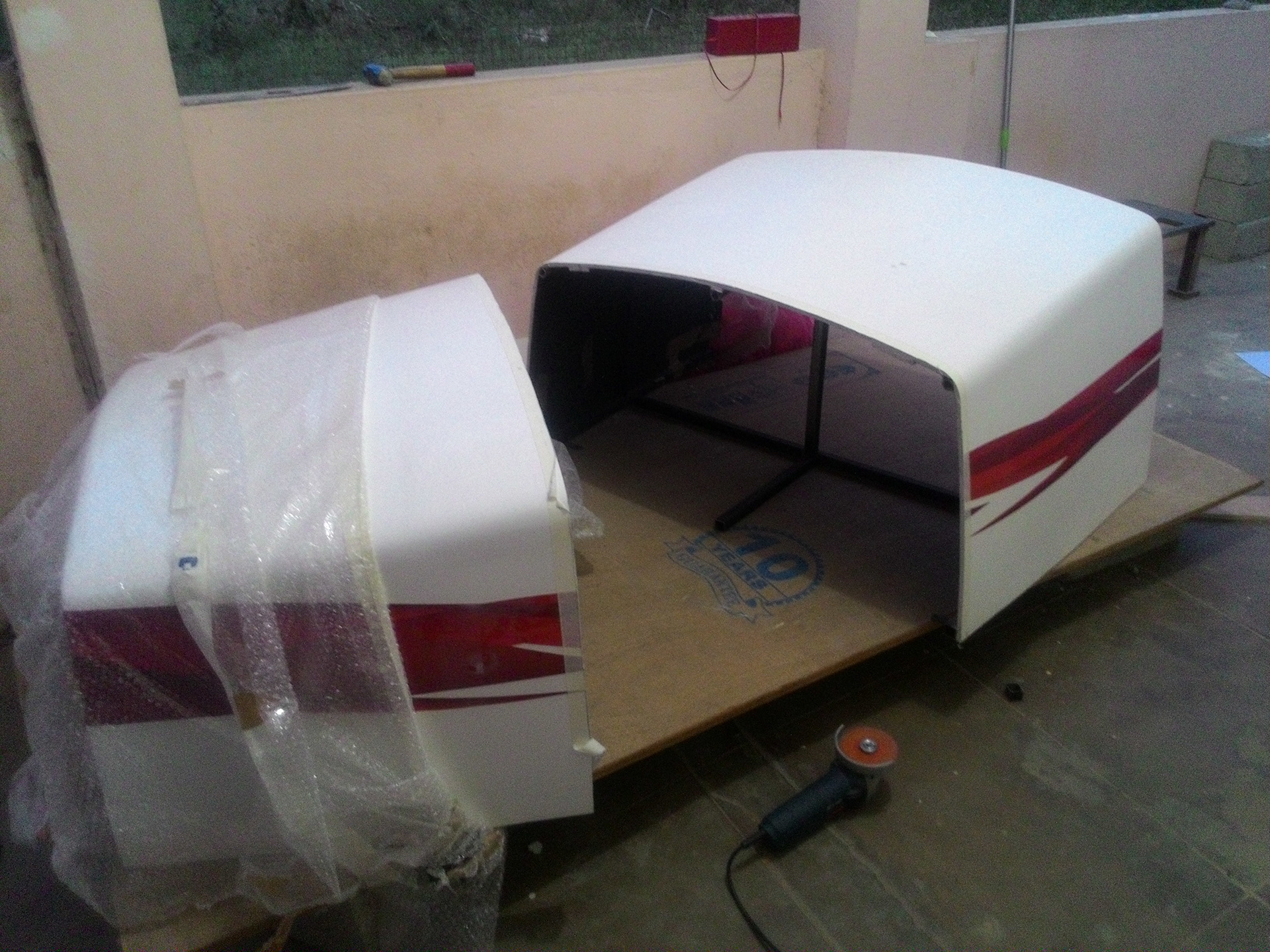
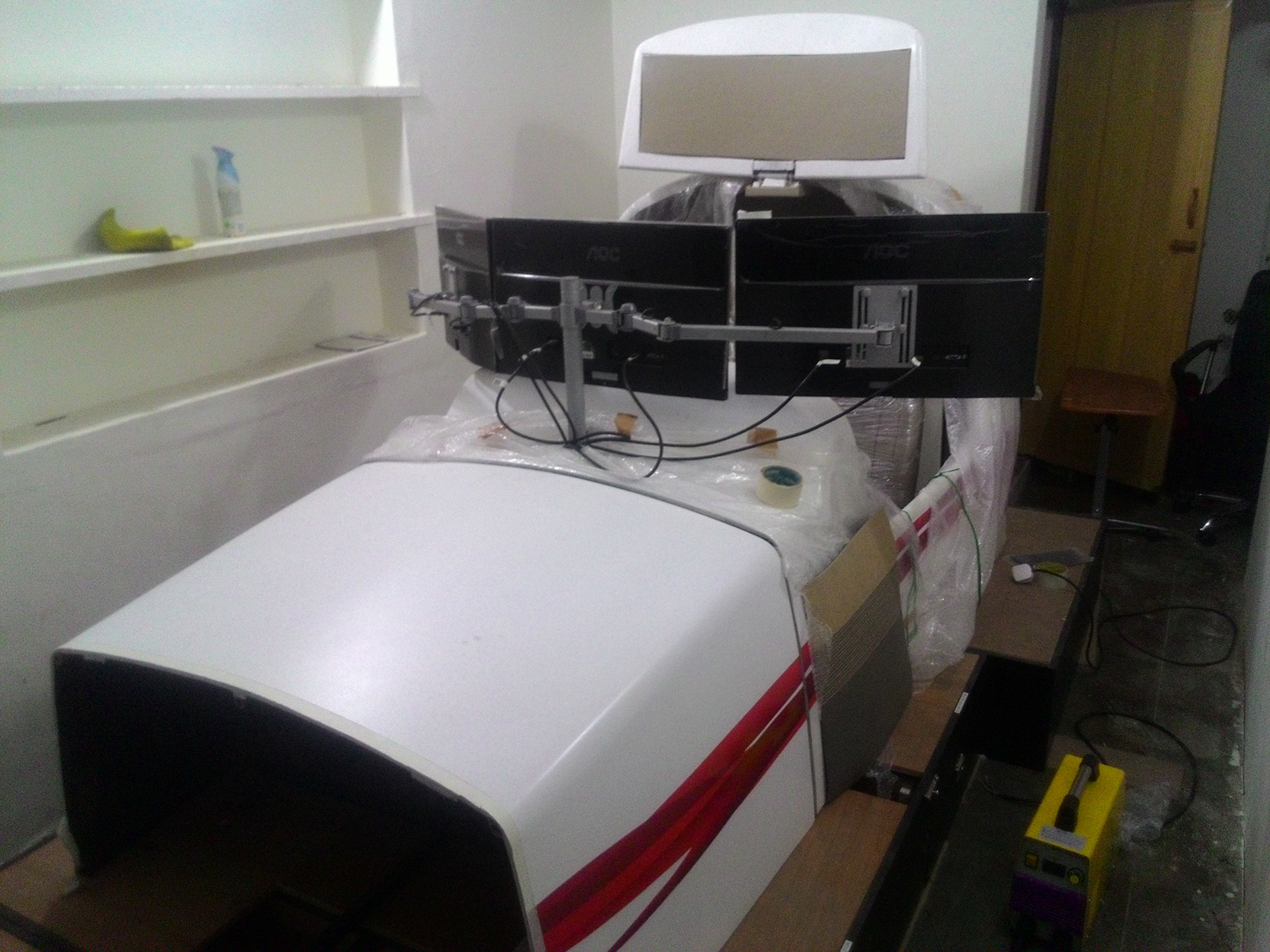
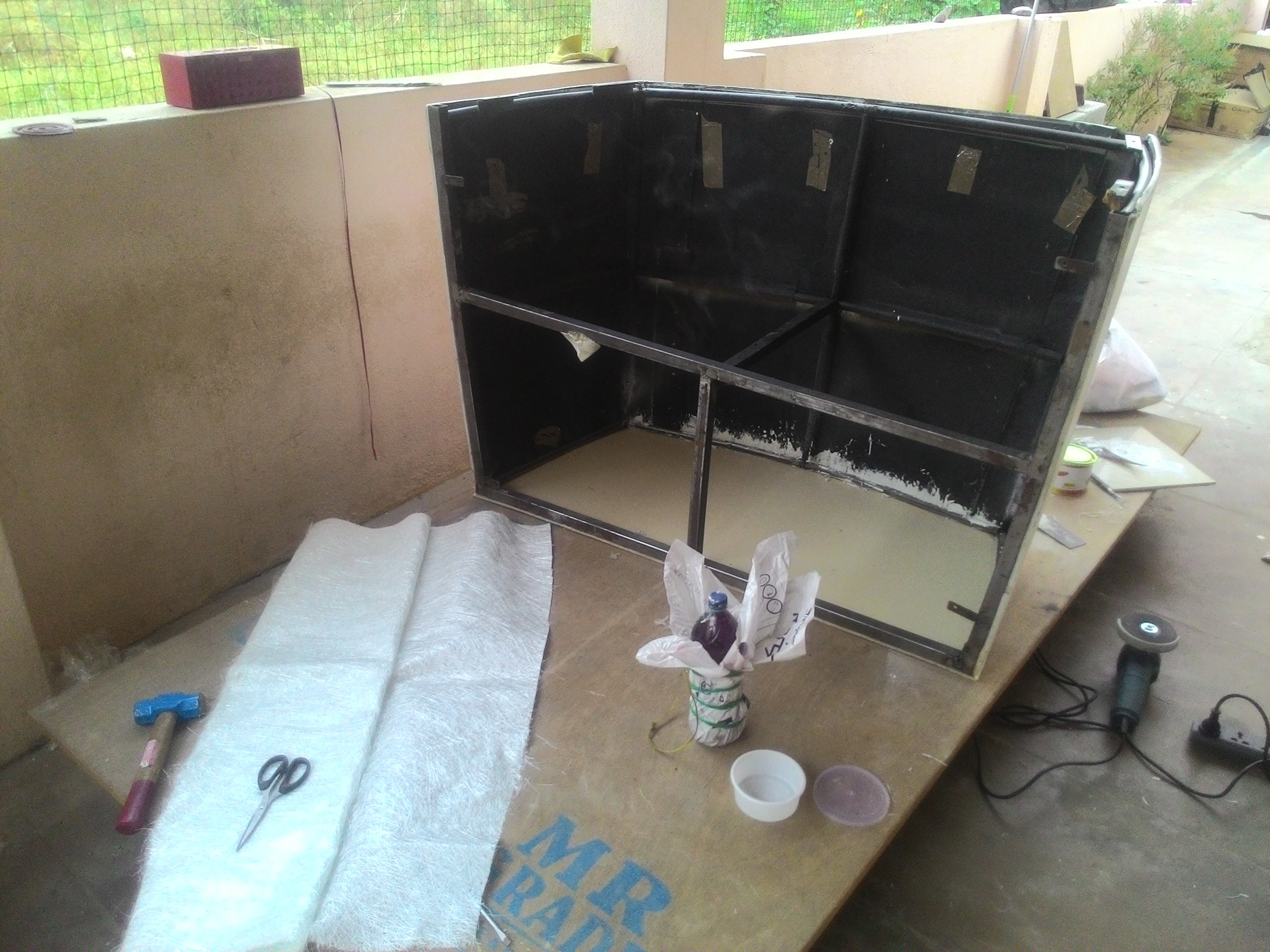

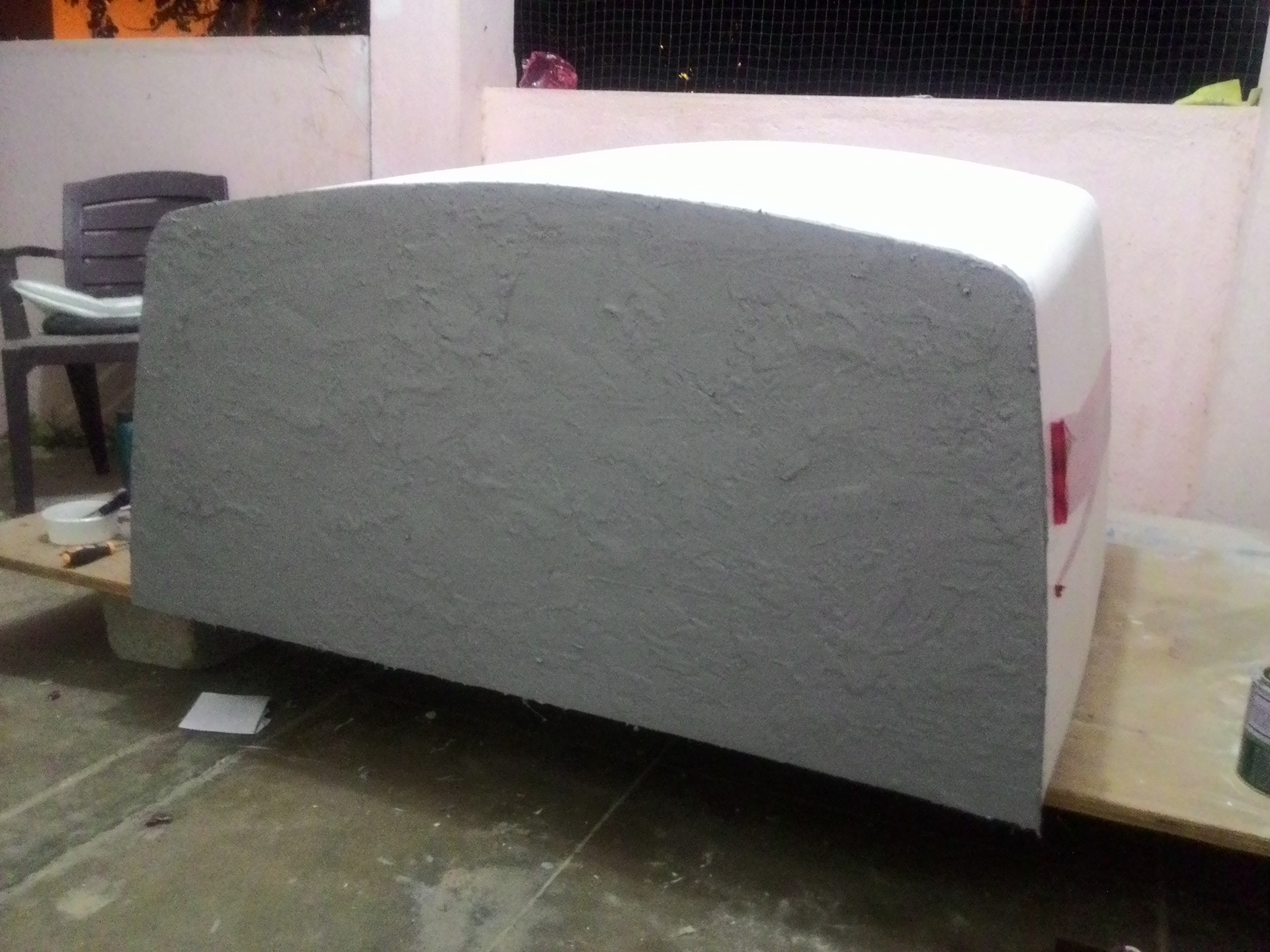
The Flight Simulator, up and running at the client's Flight School, located near Bhopal.
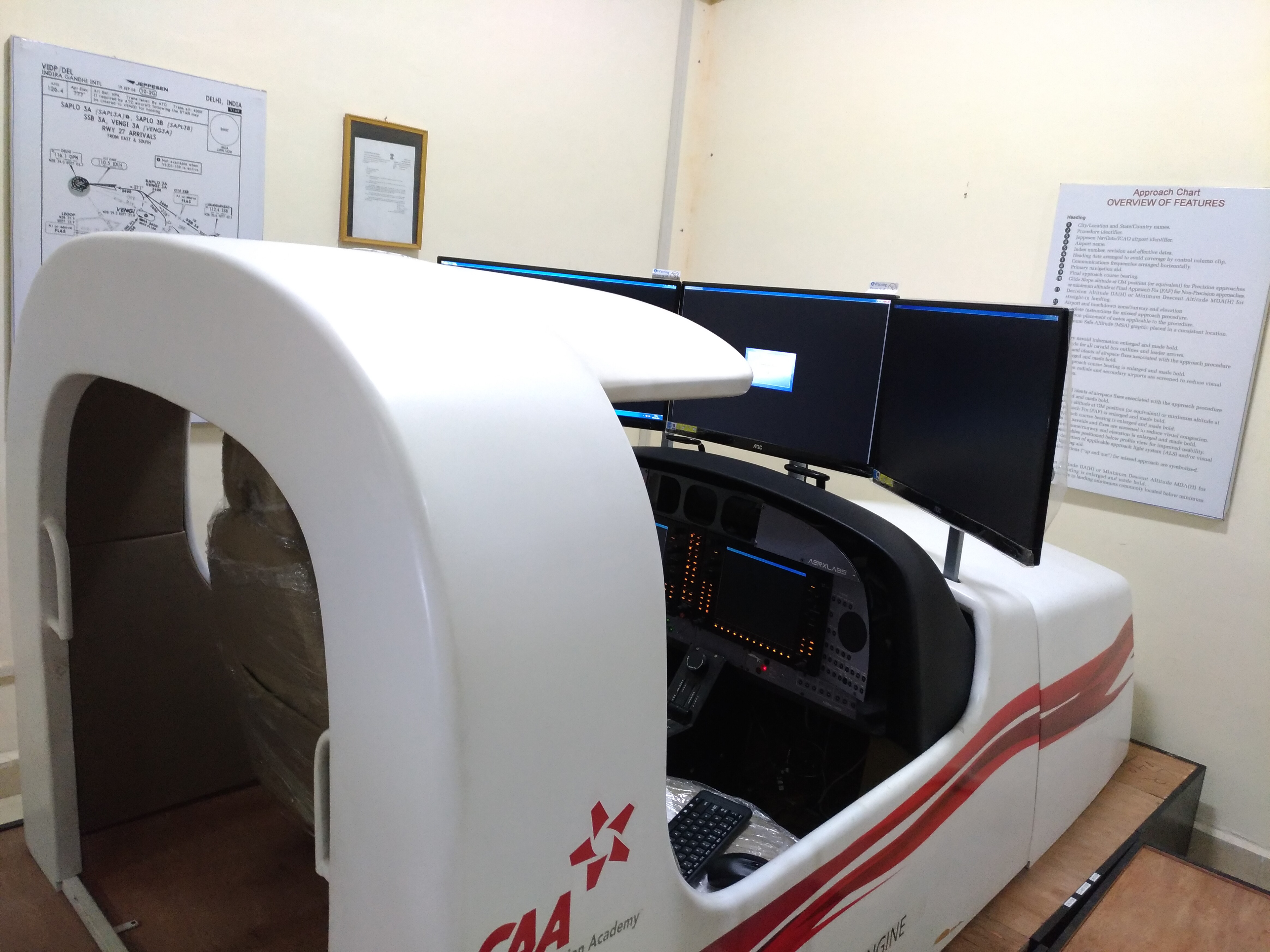

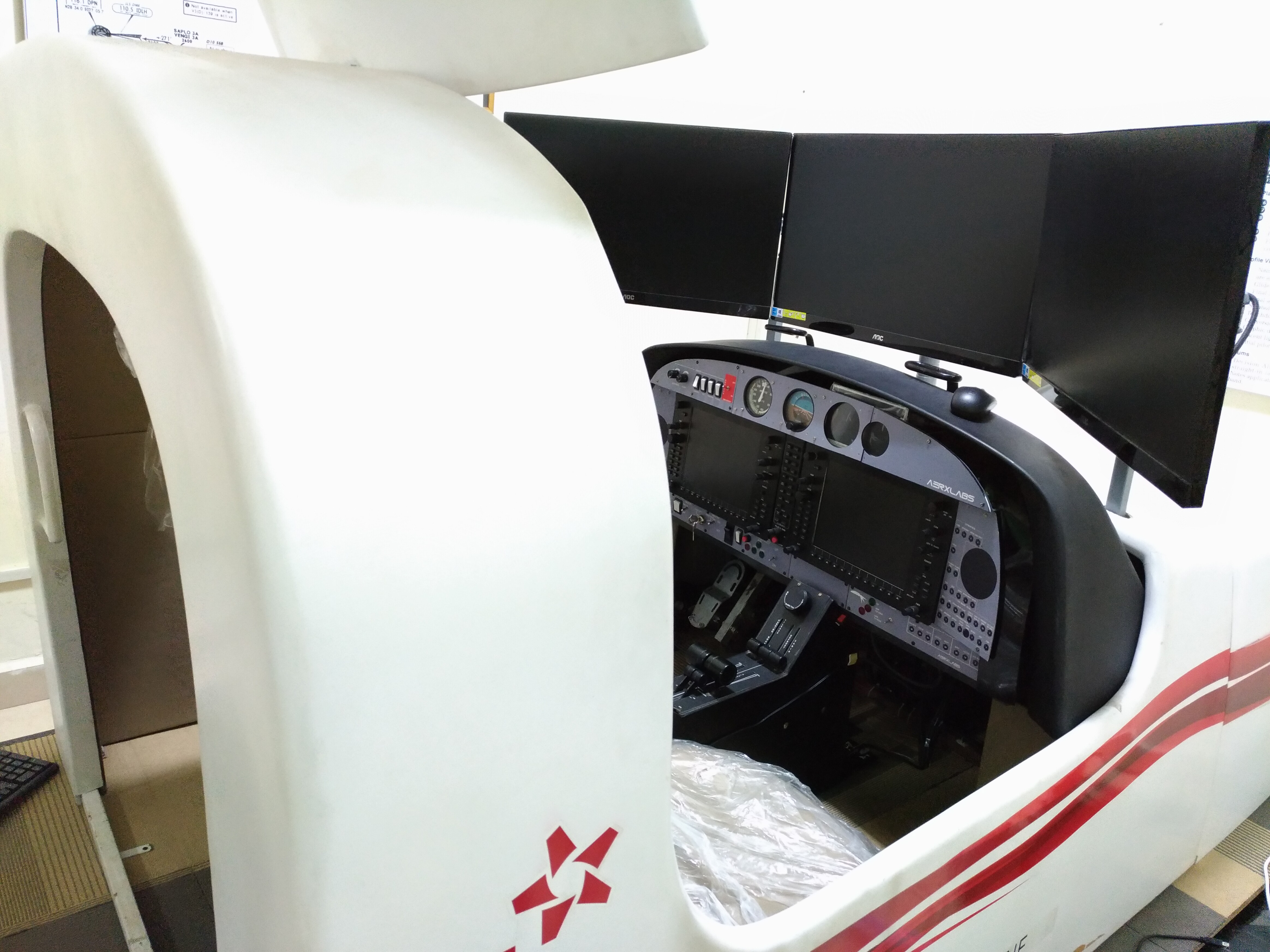
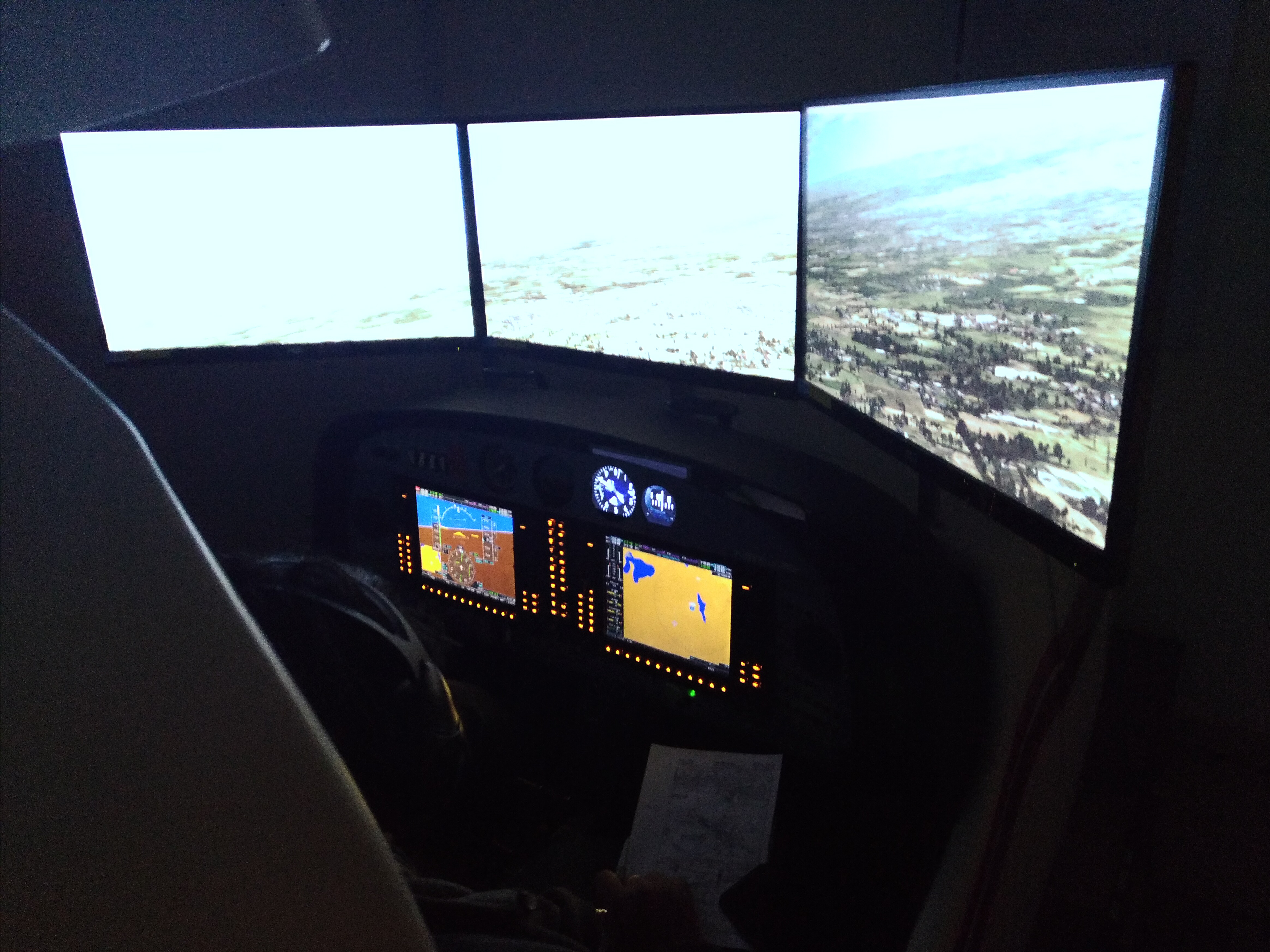

About AerX Labs
AerX Labs, a startup with interests in Experimental/Affordable Next Gen Avionics products and Flight Simulation(Flightrix) technologies. Co- founded by Sumit Rishi, Kartavya Mohan Gupta and Priyank Sharma handled this project and were also my mentors throughout.
www.aerxlabs.com
About the Team :
Designers :
Designers :
Rohit Harip, Darshan M V, Sharath H
Engineers :
Danish Malhotra, Chand Badhwar